World’s Largest Plate & Shell Heat Exchangers for Cooling in South Africa
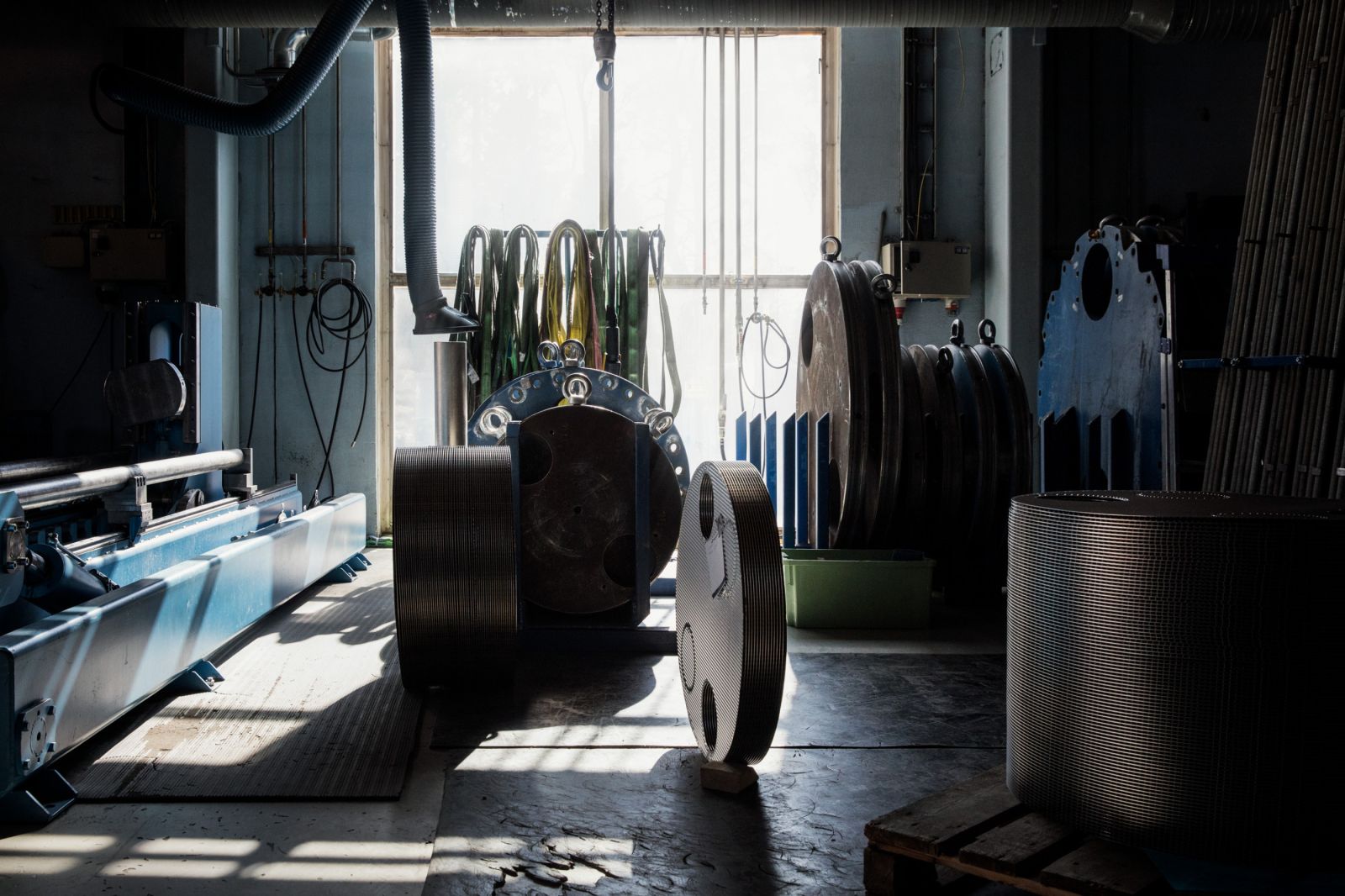
More than half of the platinum produced worldwide comes from South Africa, and Impala Platinum is the second largest platinum producer in the world. The company’s mines have several mineshafts that have been fitted with 69,000-kW ammonium cooling systems. The oldest cooling unit was installed in 1985, and the newest in 2002.
The mine’s primary cooling system is the surface cooling unit, while the secondary system involves channelling cooled service water underground. The water required by the secondary system is usually cooled during the night when the air temperature is lower and the surface cooling system is operating with a lower cooling capacity.
The surface cooling unit is a two-chamber direct-acting counterflow cooling tower equipped with drift eliminators. The system’s design flow rate is 432 litres per second. The cooled water supplied by the coolers is sprayed downwards. The water is collected in a pool from where it is pumped into water coolers and back to the surface cooling unit in a closed system.
The surface cooling unit is designed to process airflows of 400 kgs with the help of four centrifugal blowers, when the temperature of outgoing air is 7.2 °C. The surface cooling unit’s nominal cooling capacity is 15,100 kW, which can be achieved when the maximum temperature of the incoming water is 3.6 °C.
The process water is transferred to a 2,000-m2 underground cold storage unit with the aid of gravity. The water flow rate is approximately 70 litres per second.
The system also has a pre-cooling tower with a nominal cooling capacity of 4000 kW. This cooling tower lowers the temperature of the water coming back from underground as much as possible before the water goes to the water coolers. The approach temperature of the cooling tower water is approximately 2 °C.
The system is cooled by two ammonium-based Howden coolers installed side by side. The compressors are WRV-510/165-type screw compressors, both of which are powered by their own 1850 kW engines. The units are designed for a fixed volume ratio of 2.1. The older unit has a regular oil cooling system, while the newer unit has a liquid jet oil cooling system. These large screw compressors were specifically designed for the South African mining industry in the 1980s.
The nominal cooling capacity of both water coolers is approximately 8,300 kW when measured according to the evaporation temperature of -1 °C and the condensation temperature of 32 °C. The compressor engines are designed to be slightly too powerful due to the unusual operating environment. The design temperature of cooled water is 1.5 °C.
The older units require basic maintenance due to their age. In 2006, the company decided to replace all plate evaporators installed in the 1980s equipment due to signs of malfunctioning and the risk of ammonia leaks. However, replacing the evaporators, which were fitted with titanium plates, would have been an expensive process because titanium prices rose sharply in 2006 and 2007 and the delivery times were long. Titanium plates were used in the evaporators because water used in mines is often of poor quality. The evaporators are flooded evaporators, which are based on the principle of natural convection and counter-flow operation in the flow of water and liquid ammonia. Due to this, Impala Platinum decided to alter the cooling system of these mineshafts, so that cooled water would no longer be circulated underground and so that the closed circulation system would only be needed to circulate cooled water into the overground surface coolers. This modification would make it possible to replace the circulating mine water with potable water, meaning that there would be no need to continue using titanium plates.
Zonke Engineering contacted Impala Platinum and Hatch and suggested using Vahterus Plate & Shell heat exchangers in the updated system. Both Impala Platinum and Hatch were interested in the concept, but were suspicious of using ’new’ technology in such a large application.
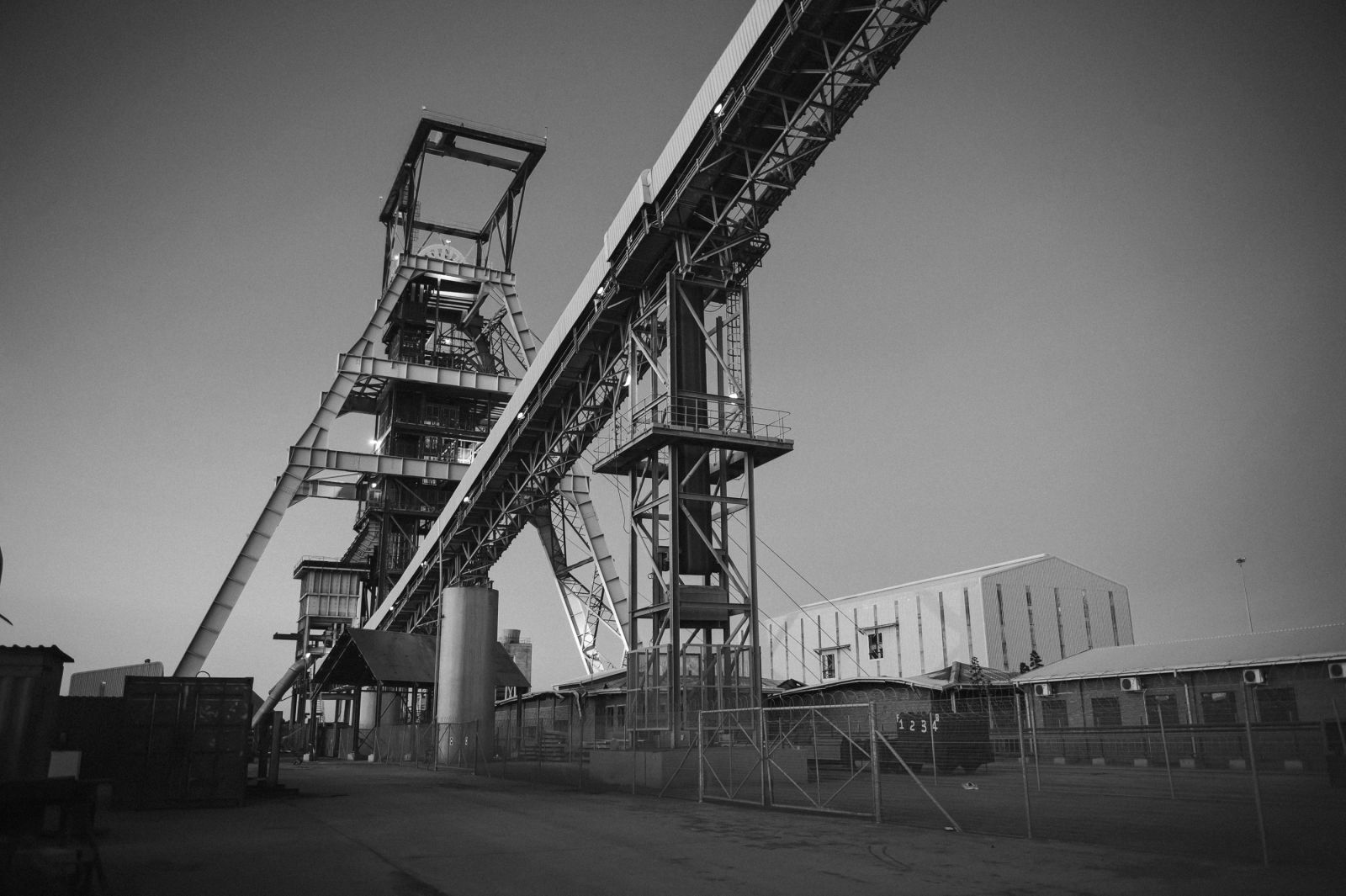
When the decision to replace the old plate coolers of the ammonia cooling units had been made, the team started to work on the selection criteria of the new heat exchangers. The new units needed to have:
- the same heat exchange capacity as the old units
- a robust structure
- ease of maintenance
- solutions that reduce the risk of ammonia leaks
- the option of using pre-existing cooling water pumps (the units’ differential pressure had to be lower than or equal to the differential pressure of the old system)
- a structure that would require as few changes to the original cooling system as possible, including piping and control devices
- a ‘universal’ structure compatible with the thermal and technical characteristics of the previously installed ammonia evaporators.
The Shell & Tube heat exchangers were excluded from the list of potential replacements due to the amount of space they need, meaning that the final list of candidates was fairly short. The last question was whether the oldest plate heat exchangers would be replaced with new similar exchangers or Plate & Shell heat exchangers. Plate & Shell heat exchangers had never before been used in a cooling application of a similar capacity or size. After careful consideration and detailed discussions with Zonke Engineering and Vahterus about potential risks, Impala Platinum and the consulting firm Hatch decided to buy Plate & Shell heat exchangers.
The system to be replaced first was the cooling system of mineshaft no 1. This system consists of two parallel ammonia cooling units with a nominal cooling capacity of 8,300 kW. The first component to be replaced was the evaporator in the oldest machine.
The cooling system of mineshaft no 1 had several unique features, including:
- Possible change in the circulation ratio of the ammonia circulatedvia an evaporator due to the circulation system of the coolant, which is based on the principle of natural convection
- Changes in water districts
- The flow rate of each cooling unit, which is half of the total flow rate of two parallel-installed cooling units, or the total flow rate when only one unit is in use. This has an impact on pressure losses and the working point of the cooling water pumps.
At first, the team decided on a size 14 Plate & Shell heat exchanger, or the largest currently manufactured heat exchanger. Due to space and weight limits, however, the team eventually selected two shorter units of the same model. The benefit of using two units is that if ammonia leaks from one of the units and reaches the water, the unit in question could be isolated from circulation and the cooling unit could run on a partial load with the help of the remaining heat exchanger.
Another benefit of the new heat exchangers was the fact that the location of the surge drum could be changed, unlike in the old units. The plate heat exchangers had an ammonia circulation ratio of 1.5. The pressure loss of the new heat exchangers was lower, which increased the coolant circulation ratio to four and above. The circulation ratio is the ratio between the total amount of a heat exchanger’s incoming coolant and the amount of evaporated coolant.
A problem that the team encountered when replacing the old heat exchanger was the fact that the plate stack of one of the exchangers did not pass the nitrogen pressure test performed on site. The faulty unit needed to be opened and the plate stack replaced with a backup stack supplied with the primary units. The plate stack was believed to have been damaged during sea transport.
Measuring the performance of the new units was of utmost importance. To run the tests, the team needed to carry out the following measures:
- Performance approval tests, which needed to be performed within 30 days of installation, when the units were still clean
- Re-calibrations and checks of all components
- Tests to confirm that the amount of oil transferred from the oil separator remained within the permissible limits
- Tests to ensure all changes made to the control devices had been made and installed correctly.
- The tests needed to be performed with both cooling units running in parallel (meaning that half of the flow rate went through one unit) and with the water flowing through one unit only.
- The test could only be passed if differences in the energy levels stayed within a 5% margin of the defined values.
The tests revealed that pressure losses on the water side were considerably larger than originally estimated, but still clearly smaller than the pressure losses of the original plate heat exchanger at the same flow rate.
It must be noted that even though design values could not quite be achieved due to the conditions at the time of the tests, the team did achieve the desired total heat transfer coefficient.
The approach temperature observed during the test was better than the planned temperature because there was less cooling capacity available during the test.
Plate & Shell heat exchangers have proved to be an excellent and safe choice for flooded evaporator applications requiring a large cooling capacity. Thanks to the lower pressure loss of Plate & Shell heat exchangers, the pump mechanism requires less electricity.
Moreover, the Plate & Shell heat exchangers also benefit from gaskets that do not need to be replaced at all, unlike plate heat exchanger gaskets. This helps bring maintenance costs down and considerably reduces the risk of ammonia leaks.
Due to the success of the installation project, Impala Platinum has launched a project to replace the plate heat exchangers in all mineshafts with Vahterus heat exchangers. As Andre Pieters, mechanical engineer at Impala Platinum commented:
”The use of PSHEs for underground cooling of the mine shafts at Impala Rustenburg mine has proven itself to be the right long-term choice. The benefits over the original Plate & Frame heat exchangers used in this application have been immense. These include almost total elimination of the maintenance that was required in terms of replacing gaskets and damaged plates of the old Plate & Frame heat exchangers. Also, the integrity of the Vahterus units has made a huge difference to ensuring a reliable and safe operation with no risk of ammonia leakage and the possible effects of this getting into the chilled air that goes underground.”
Download the case study as a PDF
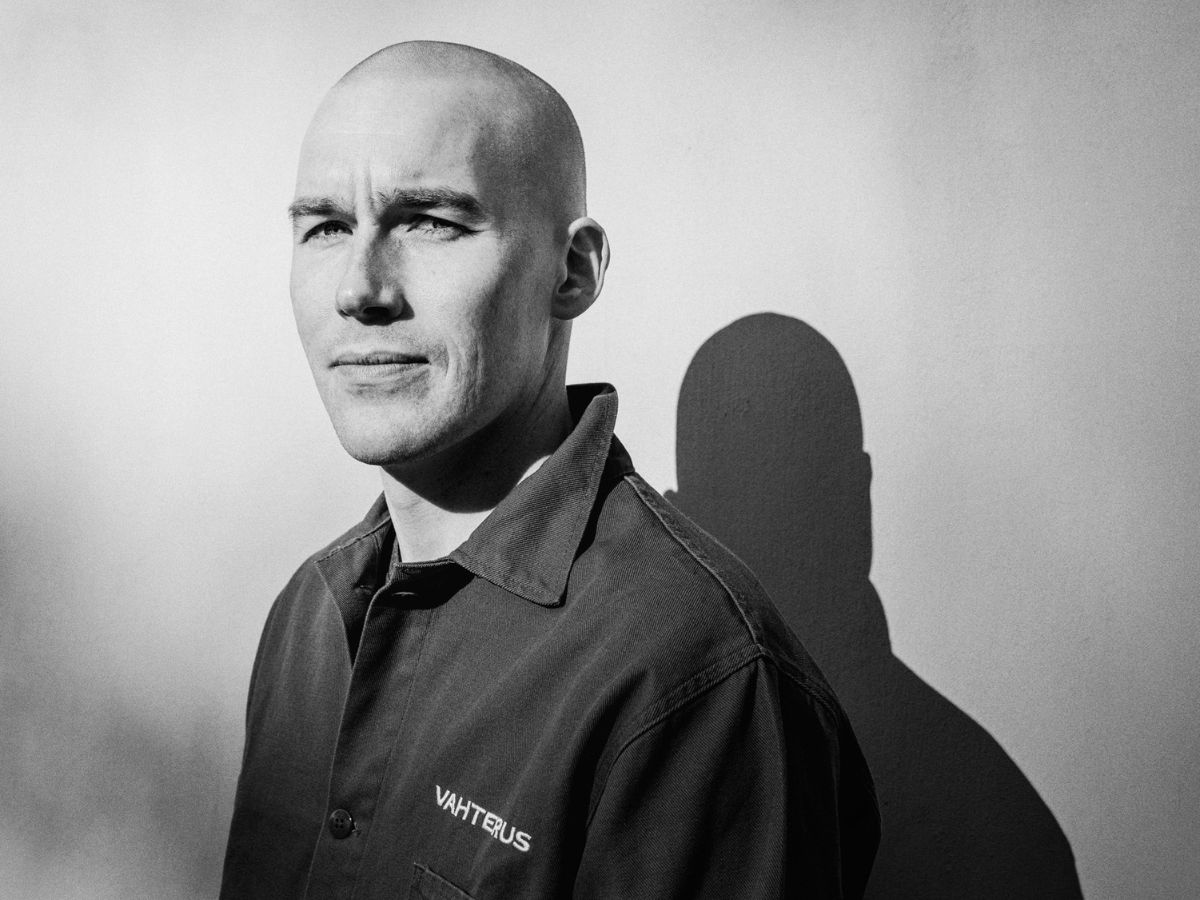
Transform your project with Vahterus Expertise
Interested in working with us? Our team of experts are ready to collaborate with you. Contact us today to embark on a journey towards cost-effective, sustainable and energy-efficient heating solutions.
Discover more of our Customer Stories
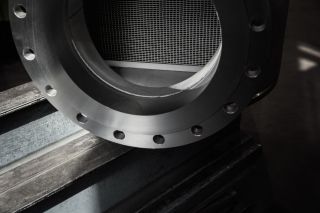
Award-Winning Heat Pumps
In 2017, Vahterus UK embarked on an innovative journey with Star Renewable Energy for the iconic Queens Quay heat network project...
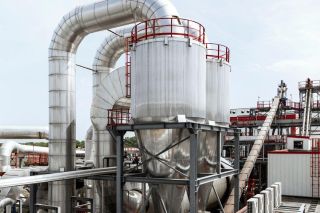
Global Challenges Drive Innovation at Pannonia Bio’s Ethanol Plant
Pannonia Bio's ethanol plant not only leads in green innovation but exemplifies collaborative success. Since 2012, the company has grown into Europe's...
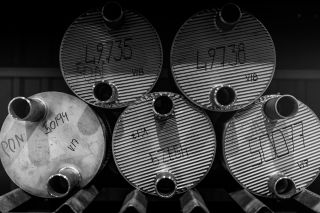
How Fermion Discovered Vahterus: 18 Years, 43 Plate & Shell Heat Exchangers
A member of the Orion Group, Fermion is a Finnish manufacturer and developer of active pharmaceutical ingredients (APIs) for Orion and other...