How Fermion Discovered Vahterus: 18 Years, 43 Plate & Shell Heat Exchangers
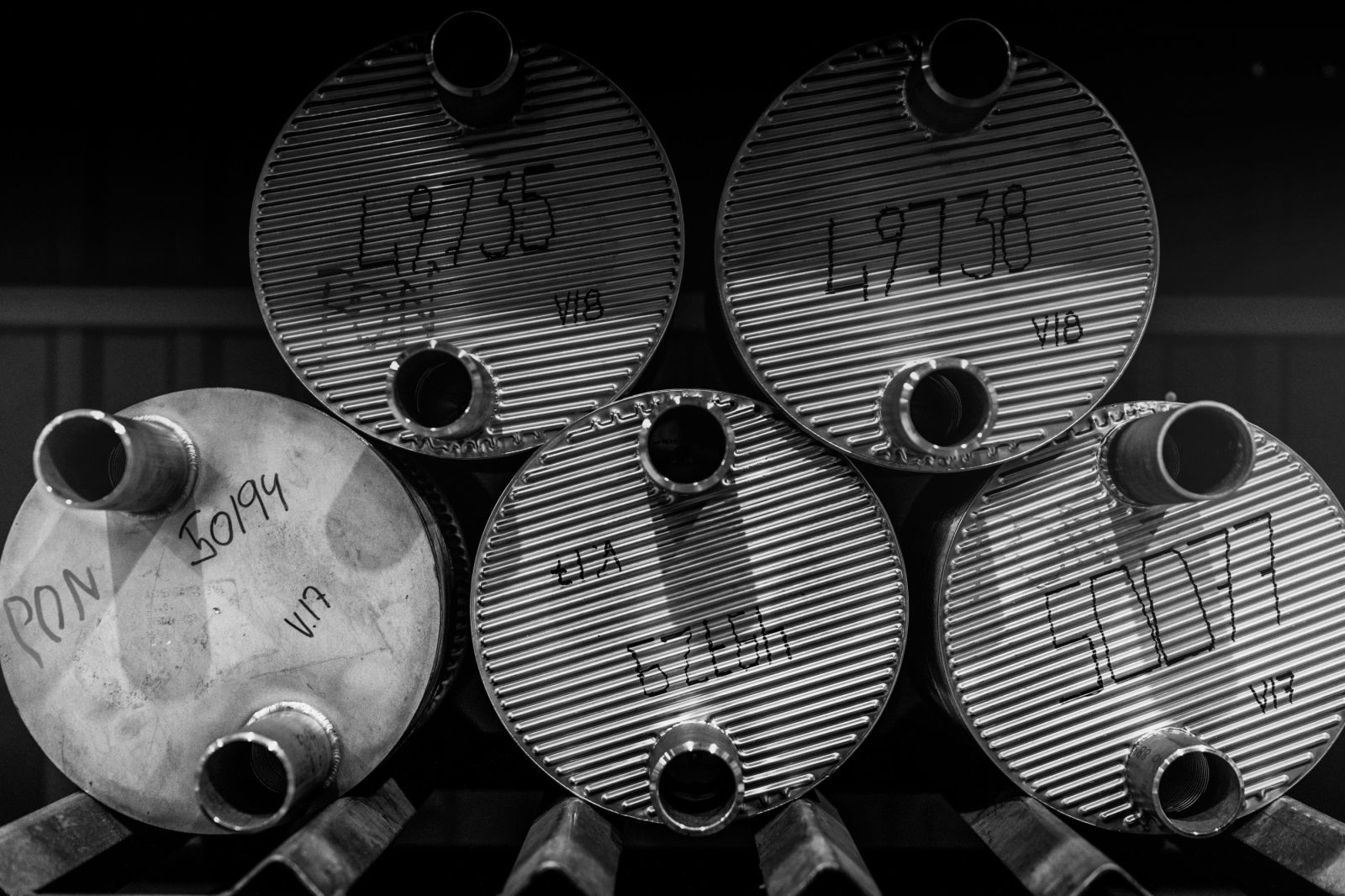
A member of the Orion Group, Fermion is a Finnish manufacturer and developer of active pharmaceutical ingredients (APIs) for Orion and other pharmaceutical companies around the world. With the special expertise and capacity to manufacture high-potency active pharmaceutical ingredients, Fermion is the global leader in some of the products it manufactures. Its plants are located in Hanko and Oulu, and its research and development facilities are in Espoo. The company’s turnover is EUR 84 million and it employs 320 people. Approximately 100 of these work in the Oulu plant.
Fermion’s chemical plant in Oulu manufactures pharmaceutical ingredients that are used in medicine for cardiovascular diseases, cancer and psychological disorders. Manufacture is input-based, and APIs are manufactured in continuous stirred-tank reactors. The reactor’s jacket is covered in pipes that have steam, water or a glycol mixture running in them to heat or cool down the reactor. The process is fully automated and the need for heating or cooling is defined by the product in question.
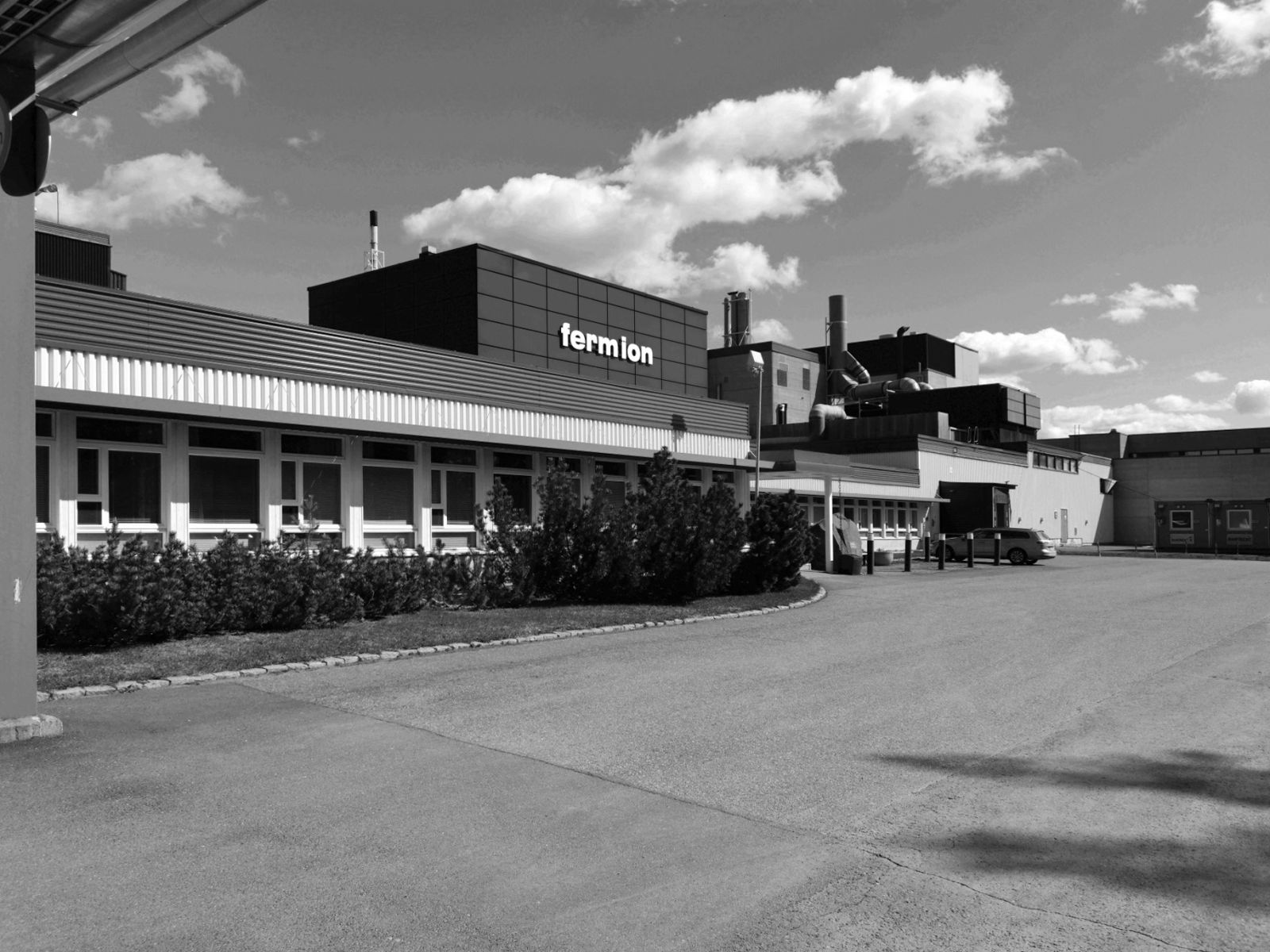
Heat exchangers heat up or cool down the plant’s manufacturing equipment – reactors, filter dryers and dryers. Each reactor requires two heat exchangers, one for heating and one for cooling. During the heating process, glycol water is heated up with steam; during the cooling process, glycol water is cooled with a mix of ethanol and water. A glycol current runs in the reactor’s jacket, providing cooling or heat depending on the input process at hand. The temperature varies from –20°C to +150°C. Due to these rapid changes in temperature, the exchanger is subjected to significant temperature shocks, several times a day. Vahterus Plate & Shell heat exchanger technology has a round plate that is designed to endure the stress caused by the rapid temperature changes.
Kai Hassinen, Fermion’s Maintenance Manager, came across Vahterus at Achema exhibition in Germany, 2001. Back then, Fermion was experiencing problems with heat exchangers and Hassinen was intrigued by the new heat-exchange technology. ‘A salesman demonstrated the construction of the Plate & Shell heat exchanger and what he said about its qualities convinced me‘, says Hassinen. ‘The plate pack isn’t welded onto the exchanger itself. That was new.’
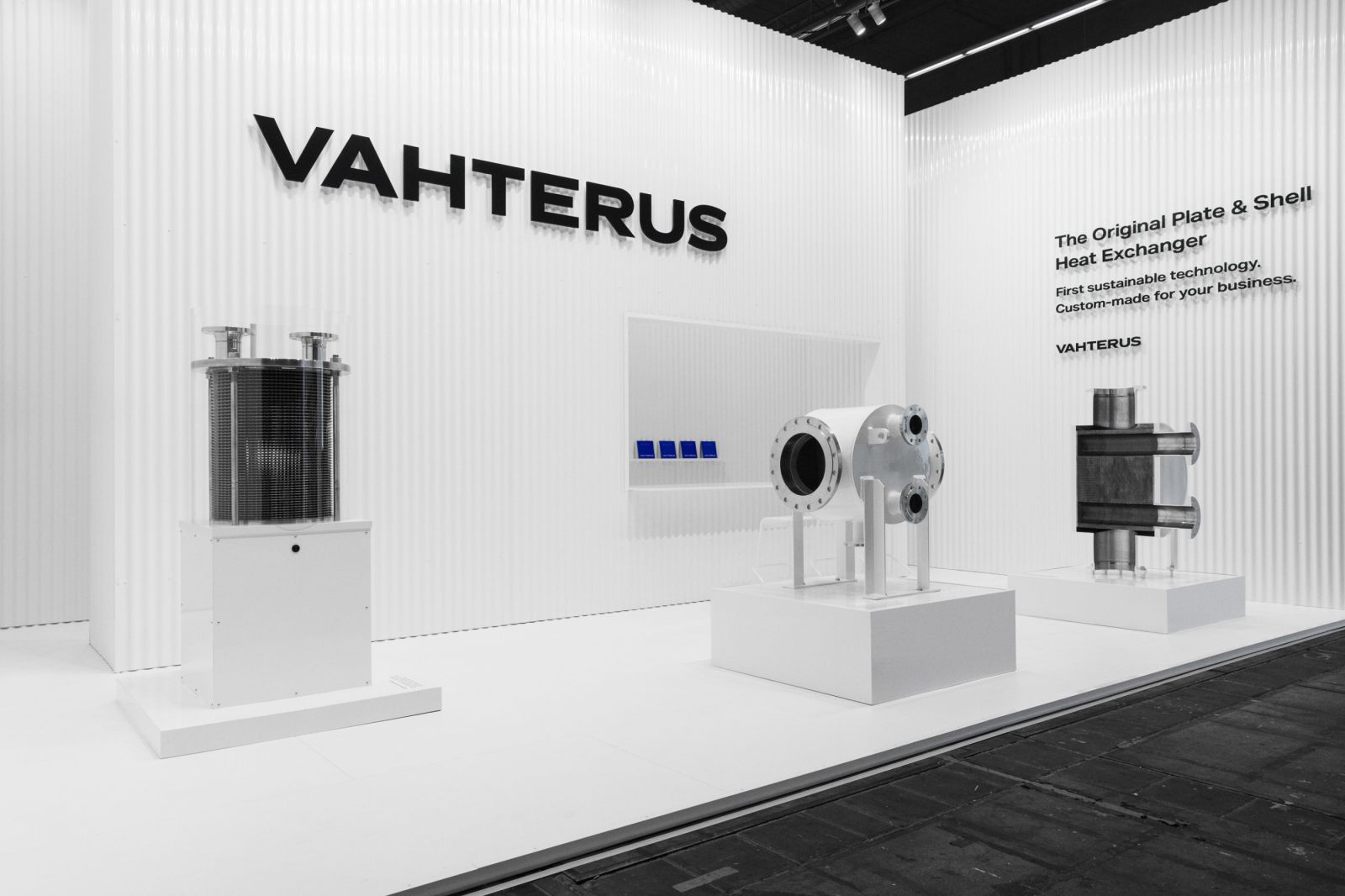
Fermion had previous experience with both gasketed and fully welded heat exchangers. Both types had been tested at the Oulu plant with poor success. ‘The problem with the previous heat exchangers was their short life span. They were functional for a while and then began to leak’, says Hassinen. The innovative product and new approach of Vahterus convinced Hassinen, and Fermion decided to test this new technology. The first Vahterus heat exchanger was installed at the Oulu plant in 2003.
Vahterus’s Plate & Shell heat exchanger met all the operational expectations and endured the conditions that other technologies could not. Following positive experiences over the years, Fermion has installed more Vahterus products to replace broken heat exchangers in their processes. The latest collective project was the expansion of the Oulu plant in spring, when Fermion equipped its new reactors with Vahterus products. ‘At the moment, we’re engaged in a renovation project where the heat exchangers of three pieces of manufacturing equipment are being renewed, six new heat exchangers in total’, says Hassinen.
The spring project was a natural continuation to Fermion’s years of collaboration with Vahterus. Currently, the firm has a total of 43 Vahterus Plate & Shell heat exchangers installed in its processes, of which not even one has started to leak. Hassinen sees no reason why all of the applicable heat exchangers shouldn’t be replaced with Vahterus products in the future.
‘We’re already planning to replace old heat exchangers with Vahterus heat exchangers’, Hassinen says. ‘We still have seven old machines with old heat exchangers at the plant. All of the old machines will be renewed and 14 new heat exchangers will be installed in the process.’
Ensuring safety is vital in the processes of a pharmaceutical plant. Therefore, the heat exchangers that are part of the heating and cooling systems must be stable. Vahterus Plate & Shell heat exchangers have endured the challenging conditions and Fermion has been pleased with the products and their operation over the years. ‘Our experience has been excellent and not a single Vahterus heat exchanger has broken down’, Hassinen sums up after nearly two decades of collaboration.
Download the case study as a PDF
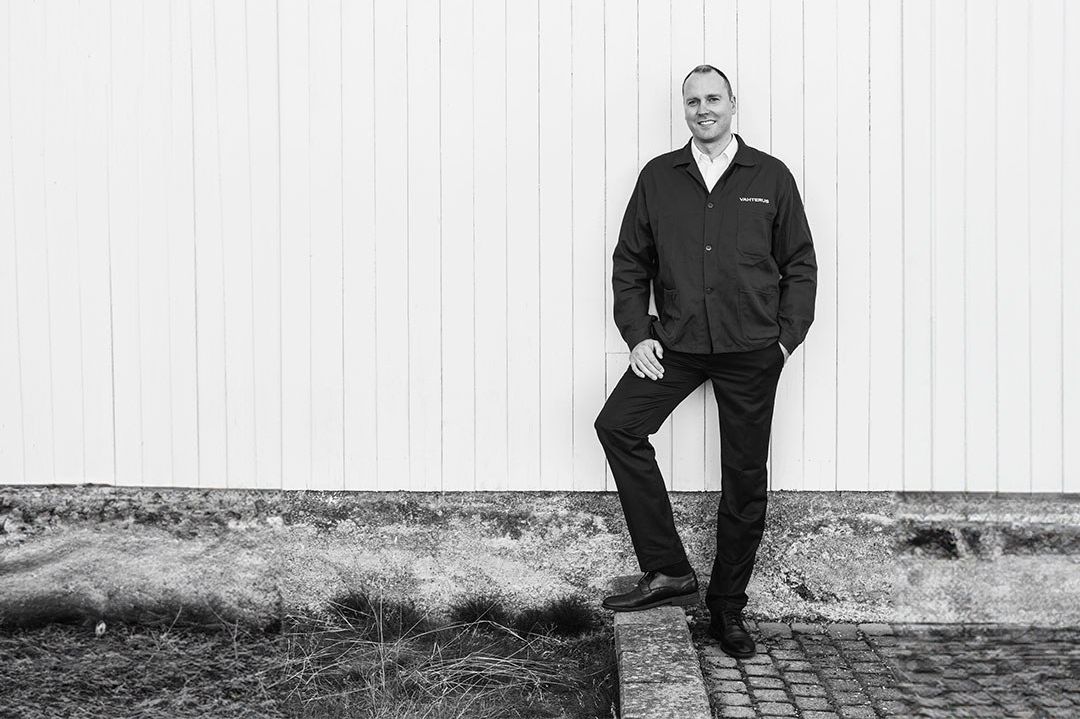
Transform your project with Vahterus Expertise
Interested in working with us? Our team of experts are ready to collaborate with you. Contact us today to embark on a journey towards cost-effective, sustainable and energy-efficient heating solutions.
Discover more of our Customer Stories
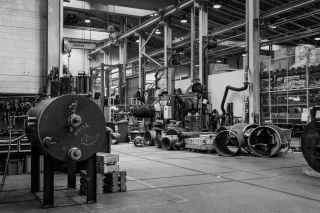
Colonial Pipeline Runs Between the Gulf Coast and the New York Harbor Area
Colonial Pipeline, headquartered in Alpharetta, Georgia, is the largest US refined products pipeline system and can carry more than three million barrels...
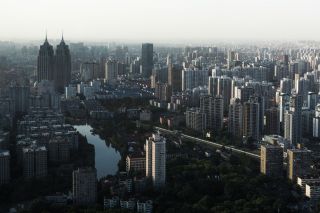
Chinese Edible Oil Refinery Plants Operate with Vahterus Heat Exchangers
Tracy Hakala, Vice President for Vahterus APAC China is famous for its wide variety of culinary options and flavours. An important element...

Cryostar’s Saturation System Transforms Truck-Fuelling Stations
Founded in 1972, Cryostar specialises in designing and manufacturing cryogenic equipment. The company offers turbomachines, gas heaters and vaporisers, pumps, turbines as...