Vahterus Heat Exchangers Meet INERATEC’s Demands for Effective Heat Recovery
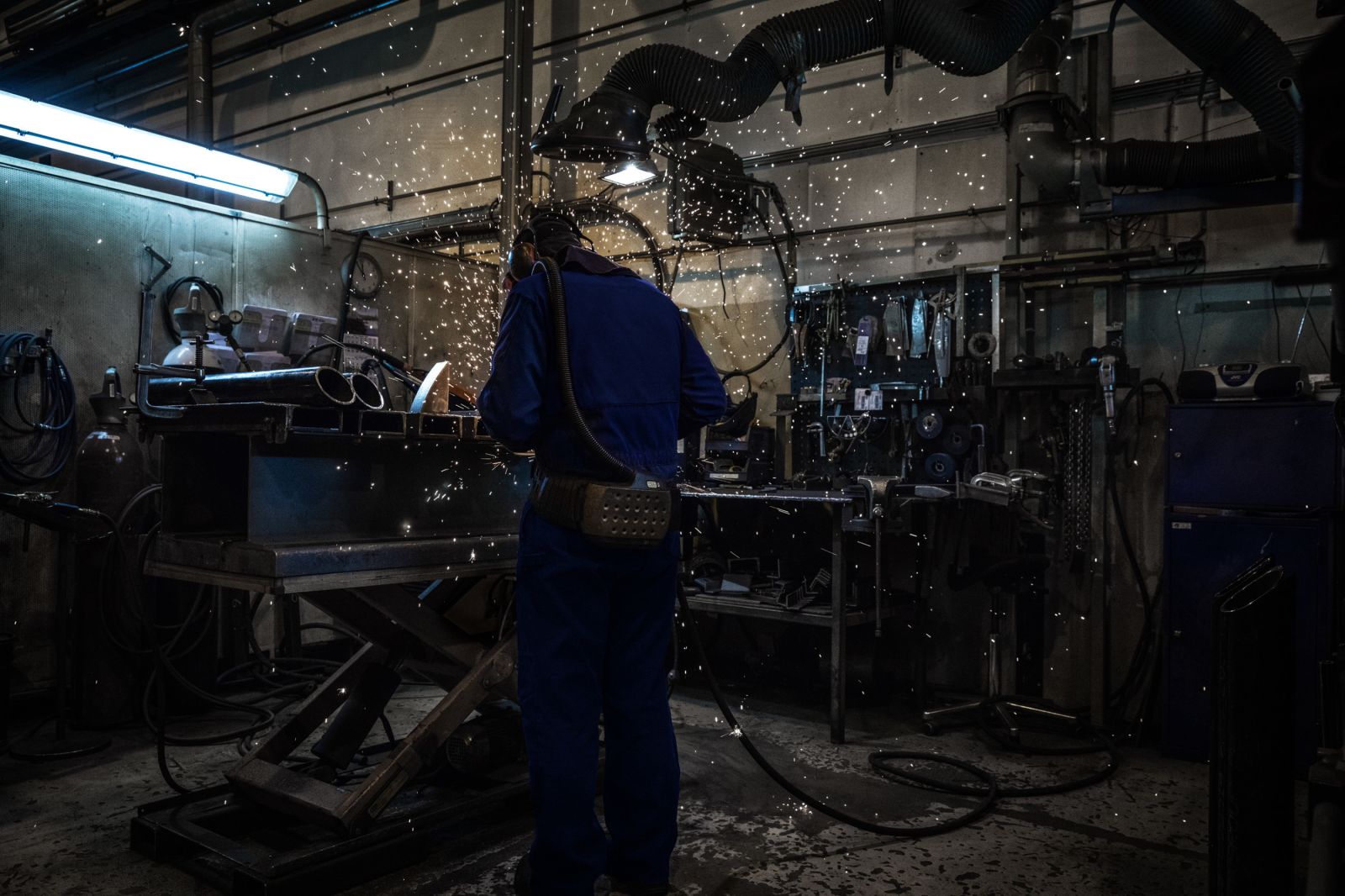
INERATEC packages compact chemical plants into containers, in which Fischer-Tropsch fuels and chemical materials are produced efficiently from various gases. Offering compact chemical systems for Gas-to-Liquid, Power-to-Liquid and Power-to-Gas processes, INERATEC utilises innovative technology, based on compact microstructured chemical reactors. These enable the integration of an entire chemical plant into transportable containers. Their compact reactor technology allows dynamic, safe and efficient operation of highly exothermic and endothermic chemical reactions, such as Fischer-Tropsch synthesis. Significant competitive advantages arise due to the decentralised scale, with INERATEC providing services ranging from engineering and construction to the commissioning and maintenance of the units.
In the INERATEC Gas-to-Liquid, Power-to-Liquid and Power-to-Gas processes, the compact and intelligent design of heat exchangers is essential for high thermal efficiency. Heat recovery and compact heating, as well as cooling at different points within the synthesis process are key design features in the container-sized plants.
One example of the successful integration of Vahterus PSHEs into an INERATEC chemical plant design is the Power-to-Liquid process currently operated at INERATEC’s site in Karlsruhe, Germany. Prior to this, in 2017, this technology was successfully trialled in field tests in Helsinki and Lappeenranta, Finland, with Vahterus’s partner, VTT Technical Research Centre of Finland.
In the Power-to-Liquid process, CO2 and renewable H2 are converted in a two-stage synthesis process to produce liquid Fischer-Tropsch fuels, as well as valuable chemical products. In the first step, CO2 and H2 are converted in a Reverse Water Gas Shift reactor into a synthesis gas mixture. The following FT reaction step then converts the synthesis gas into the desired chemical products.
The most important demands of heat exchangers in this process, within the containerised unit, are compact size, the ability to process the streams at high temperatures up to 500°C and high pressure up to 30 bar. Additionally, the heat exchangers must be durable and reliable, due to the flammable gases, such as H2 and light hydrocarbons, that are present in the synthesis process.
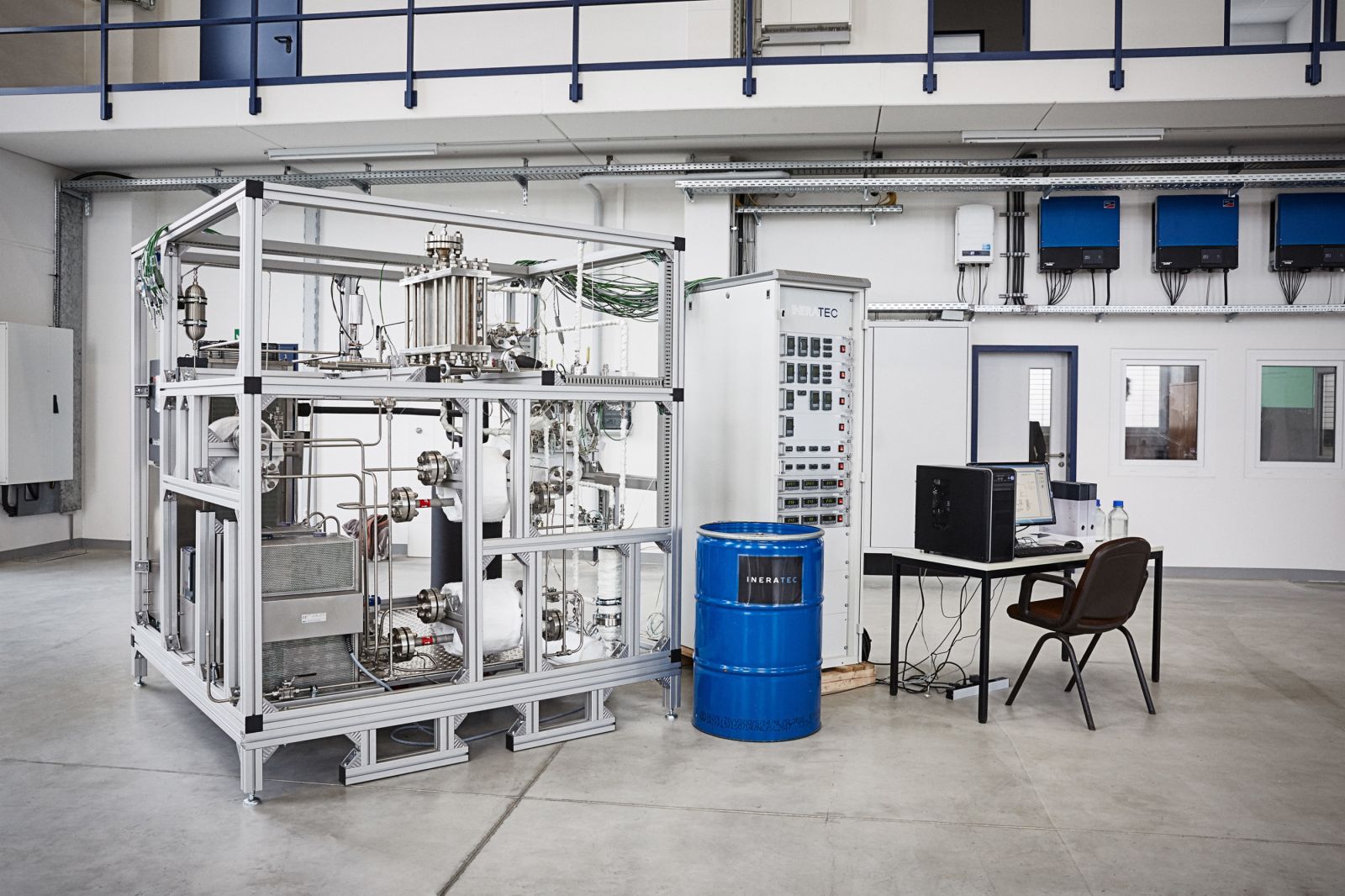
INERATEC decided to use six Vahterus PSHEs for the Power-to-Liquid demonstration plant, to provide efficient and compact heating and cooling at different points in the process. Vahterus PSHEs provide highly efficient and safe operation within the containerised chemical plants.
INERATEC looks forward to the continuation of its successful partnership with Vahterus on upcoming projects. PSHEs meet the INERATEC’s high demands for process efficiency and effective heat recovery. For upcoming larger scale Power-to-Liquid units, INERATEC has already ordered further Vahterus PSHEs.
Download the case study as a PDF
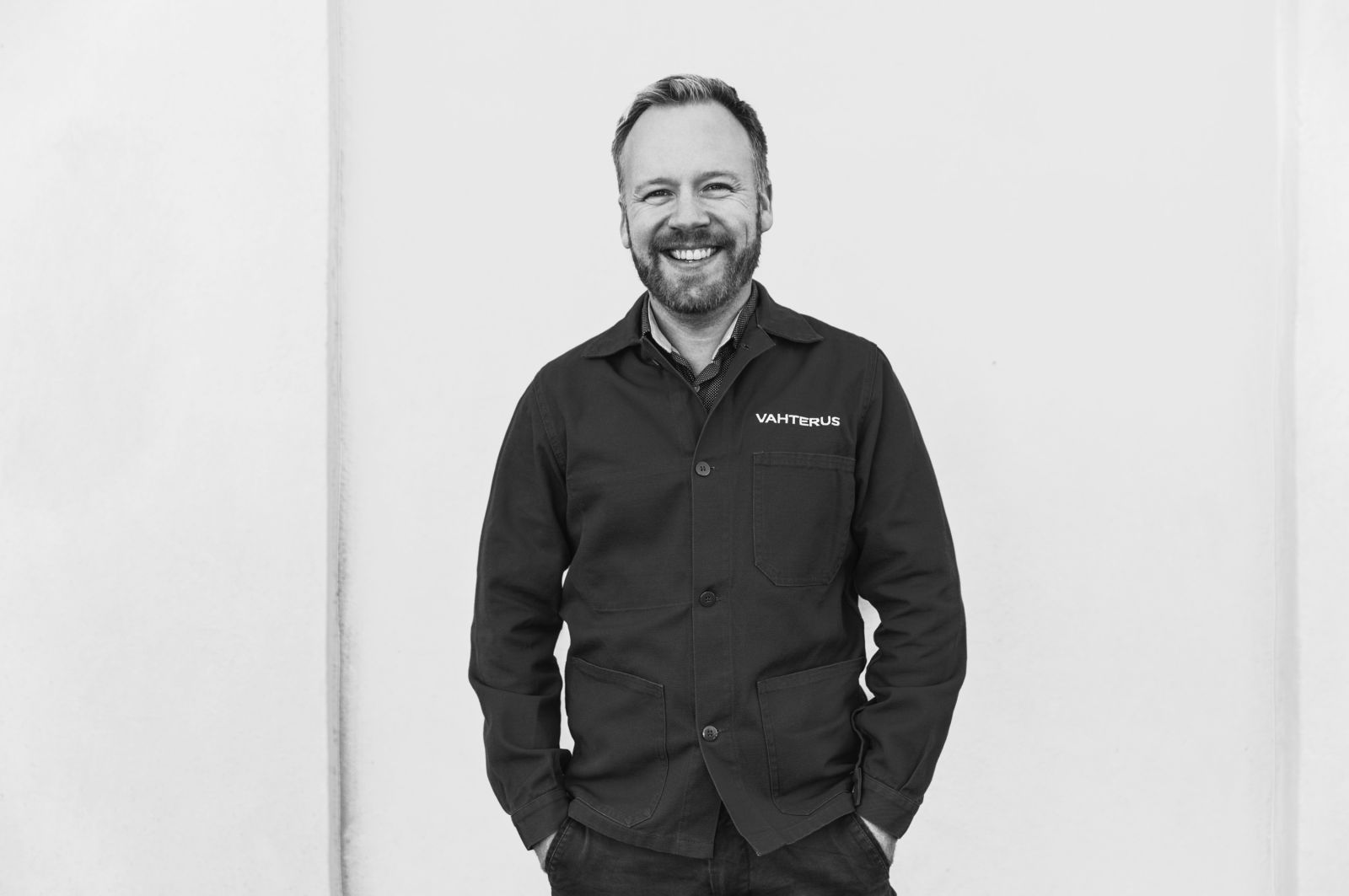
Transform your project with Vahterus Expertise
Interested in working with us? Our team of experts are ready to collaborate with you. Contact us today to embark on a journey towards cost-effective, sustainable and energy-efficient heating solutions.
Discover more of our Customer Stories
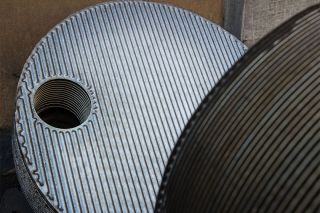
NH3 Recovery System in Richards Bay, South Africa
Omnia Limited is a manufacturer of chemicals and specialist products for the chemical, mining and agricultural industries. The Omnia industrial complex is...
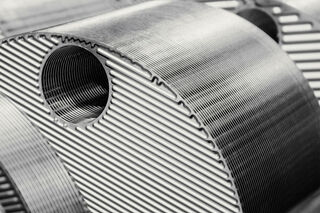
Waste Heat Recovery with Vahterus PSHE
The petrochemical and refining industry is a very energy intensive field and is under constant pressure to increase energy efficiency and...
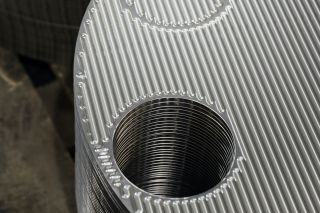
Recovery of Heat from Vapour Produces Savings at a Tyre Factory in China
A South Korean tyre manufacturing company has production facilities in Chongqing, China. The manufacturing process requires an air separator for discharging air...