New Type of Reactor Cooler for BASF Polyol Plants
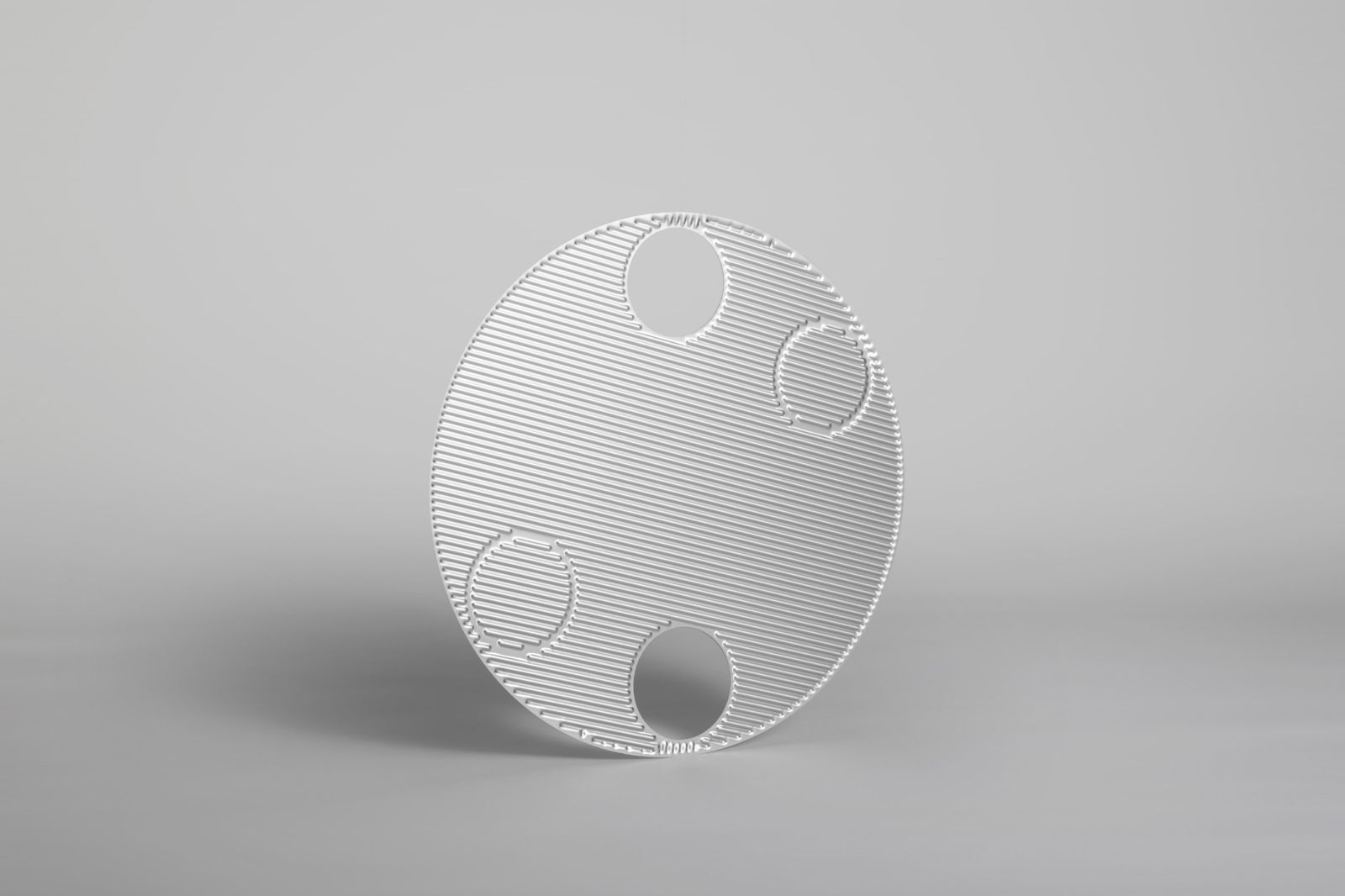
BASF ‘The Chemical Company’, one of Vahterus’ biggest clients in the Chemical Industry, is the world leader in the processing of polyurethanes. In collaboration with Vahterus, BASF global engineering department, based in Ludwigshafen, Germany, found that the Plate & Shell Heat Exchanger (PSHE) was the perfect solution for its challenging reactor cooling duties in its Polyol plants. Today, Vahterus’ PSHEs are in operation at BASF’s Polyol plants in Asia, Europe and most recently in North America.
Polyol is a chemical intermediate in the polyurethane process. The base materials are ethylene oxide, propylene oxide and glycerin. These are mixed in a reactor along with other media. With the help of a catalyst, exothermic polymerisation is initiated in the reactor and there is the need to remove the heat of the reaction. Since the viscosity of the Polyol is relatively high, gasketed exchangers cannot be used. The PSHE, however, is a fully welded heat exchanger and thus perfect for the job. Batch process cooling duties, such as in the Polyol process, require heat exchangers that can handle thermal cycling. The operating temperatures in the heat exchanger change radically during the day, which can be problematic for a traditional block-type heat exchanger, and result in thermal fatigue problems. The circular geometry of PSHE plates offers excellent resistance to thermal cycling.
BASF noted numerous benefits of PSHEs in the polyol reactor cooling service, some of which include:
- Reduced risk of leakage due to PSHE’s ability to withstand temperature shock and thermal cycling
– Access to welding seams of the plate pack for quality control and assurance during fabrication
- Openable and resistant shell construction allowing removal of plate pack
- Effective draining of the product
- Very compact design, based on the high thermal efficiency of PSHE
with 7 MW heat of reaction removed in a single exchanger
- Commercially attractive compared to other compact plate heat exchangers
The installation of PSHE at BASF Geismar (USA) in 2007 was part of its Polyol Expansion Project. With this investment, Polyol production capacity was increased from 250,000 tons to 350,000 annually. This was achieved by constructing two new reactors and extending the capacity of the two existing reactors. PSHEs are used to cool both the new and old reactors.
Download the case study as a PDF
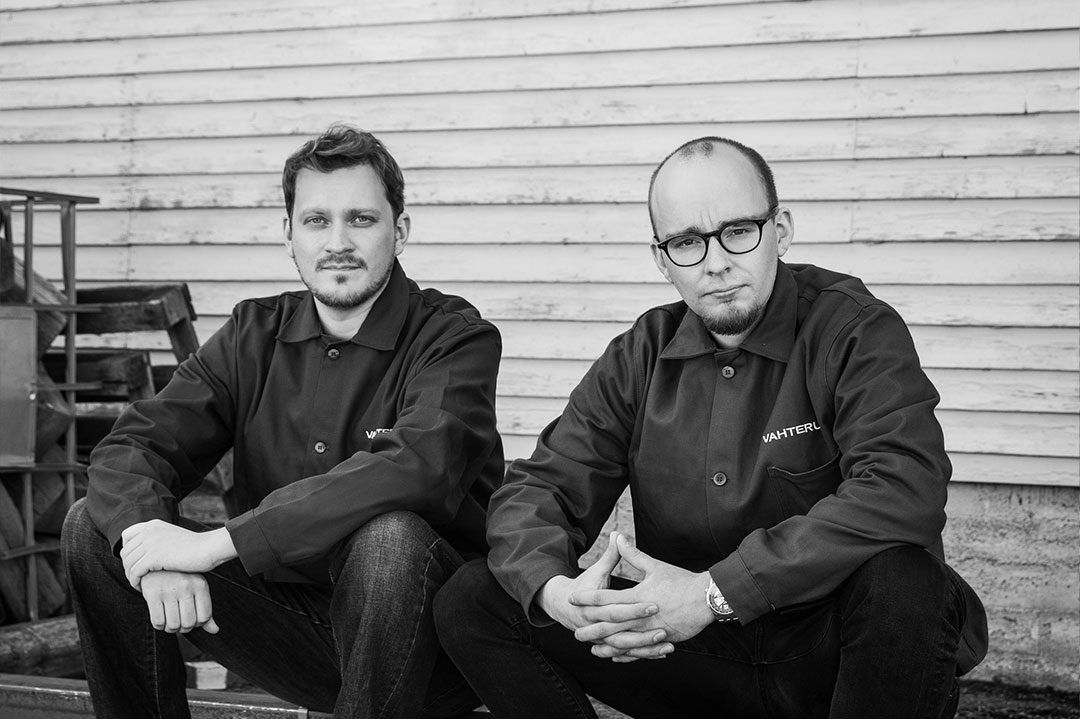
Transform your project with Vahterus Expertise
Interested in working with us? Our team of experts are ready to collaborate with you. Contact us today to embark on a journey towards cost-effective and energy-efficient heating solutions.
Discover more of our Customer Stories
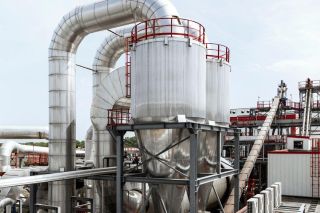
Global Challenges Drive Innovation at Pannonia Bio’s Ethanol Plant
Pannonia Bio's ethanol plant not only leads in green innovation but exemplifies collaborative success. Since 2012, the company has grown into Europe's...
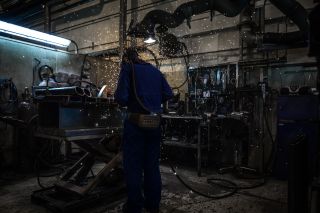
Vahterus Heat Exchangers Meet INERATEC’s Demands for Effective Heat Recovery
INERATEC packages compact chemical plants into containers, in which Fischer-Tropsch fuels and chemical materials are produced efficiently from various gases. Offering compact...

Cryostar’s Saturation System Transforms Truck-Fuelling Stations
Founded in 1972, Cryostar specialises in designing and manufacturing cryogenic equipment. The company offers turbomachines, gas heaters and vaporisers, pumps, turbines as...