NH3 Recovery System in Richards Bay, South Africa
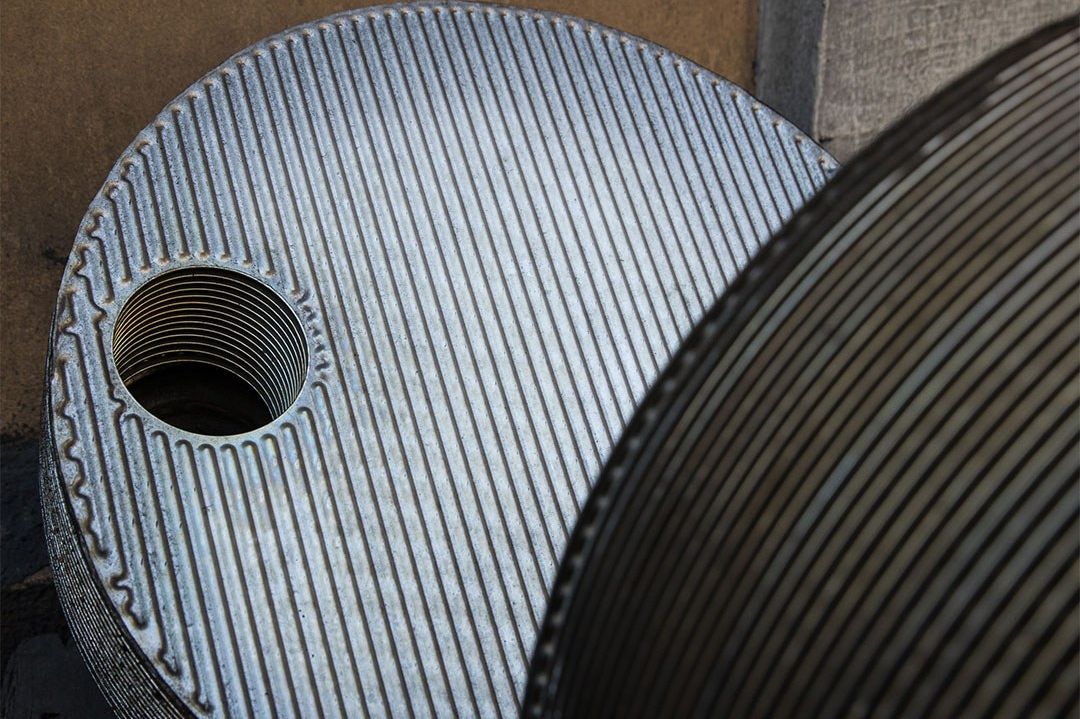
Omnia Limited is a manufacturer of chemicals and specialist products for the chemical, mining and agricultural industries.
The Omnia industrial complex is situated in Sasolburg, Free State, in South Africa, and consists of a nitric acid plant, ammonium nitrate (liquid) plant and porous ammonium nitrate (solids) plant.
Within this complex, the most important and primary feedstock for the production of nitric acid and ammonium nitrate, is ammonia. Omnia’s nitrate and ammonium plants in Sasolburg are supplied with imported ammonia and Omnia operate an ammonia off-loading station in Richard’s Bay, KwaZulu-Natal North, a few kilometres from the Richards Bay Harbor.
The economiser, droplet separator, oil coolers and condensers for the ammonia off- loading station in Richard’s Bay were manufactured by Vahterus and supplied to a refrigeration specialist company, Howden Africa, through Zonke Engineering South Africa. The Engineering, Procurement and Construction Contract (EPC) was originally the responsibility of ThyssenKrupp Industrial Solutions India (TKIS-India), with the contract later transferred to ThyssenKrupp Industrial Solutions in South Africa (TKIS-SA).
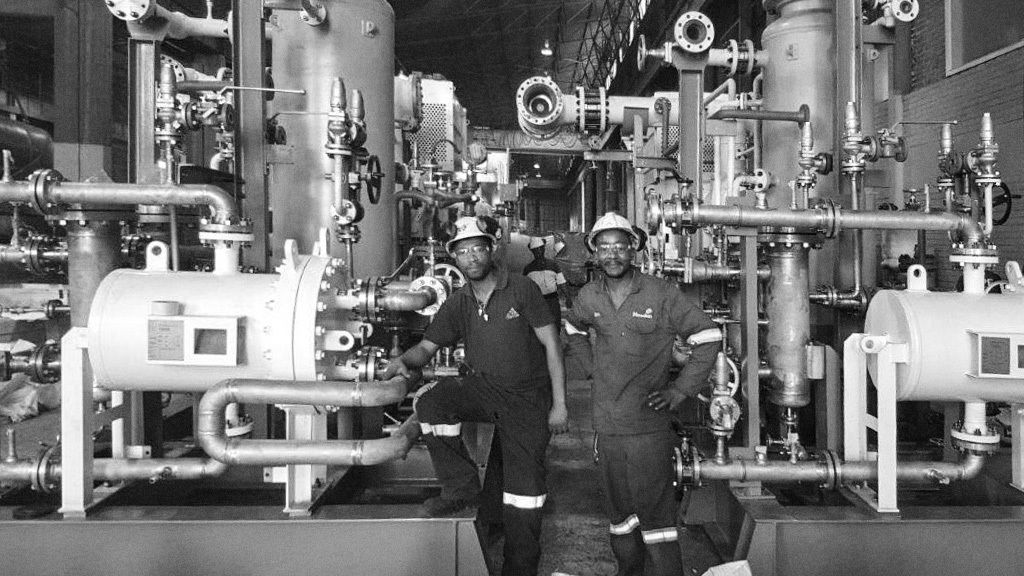
TKIS-India initially specified Shell and Tube (S&T) heat-exchanger technology for the ammonia recovery system. TKIS-SA, in consultation with Zonke Engineering, the local agents of Vahterus in Sub Saharan Africa, reviewed the heat-exchanger technology and switched to Vahterus Plate & Shell Heat Exchangers (PSHEs) due to the significant cost, schedule and performance benefits that PSHE can provide vs. Shell & Tube in this application.
TKIS-SA and Howden Africa have many years of experience in using Vahterus PSHE technology, formerly introduced to them by Zonke Engineering.
The key benefits of using Vahterus heat exchangers for ammonia recovery systems:
- Compact design and significant space-saving in the skid assembly
- Higher performance efficiency due to true counter-current flow and reliable operation
- Lower investment costs compared to Shell & Tube heat exchangers
- Ease of maintenance, with a lower maintenance frequency
- Lower total cost of ownership
- A much lower weight exchanger compared to a conventional S&T Heat Exchanger
- Ease of transportation and installation on site
- Shorter scheduled delivery than S&T
Download the case study as a PDF
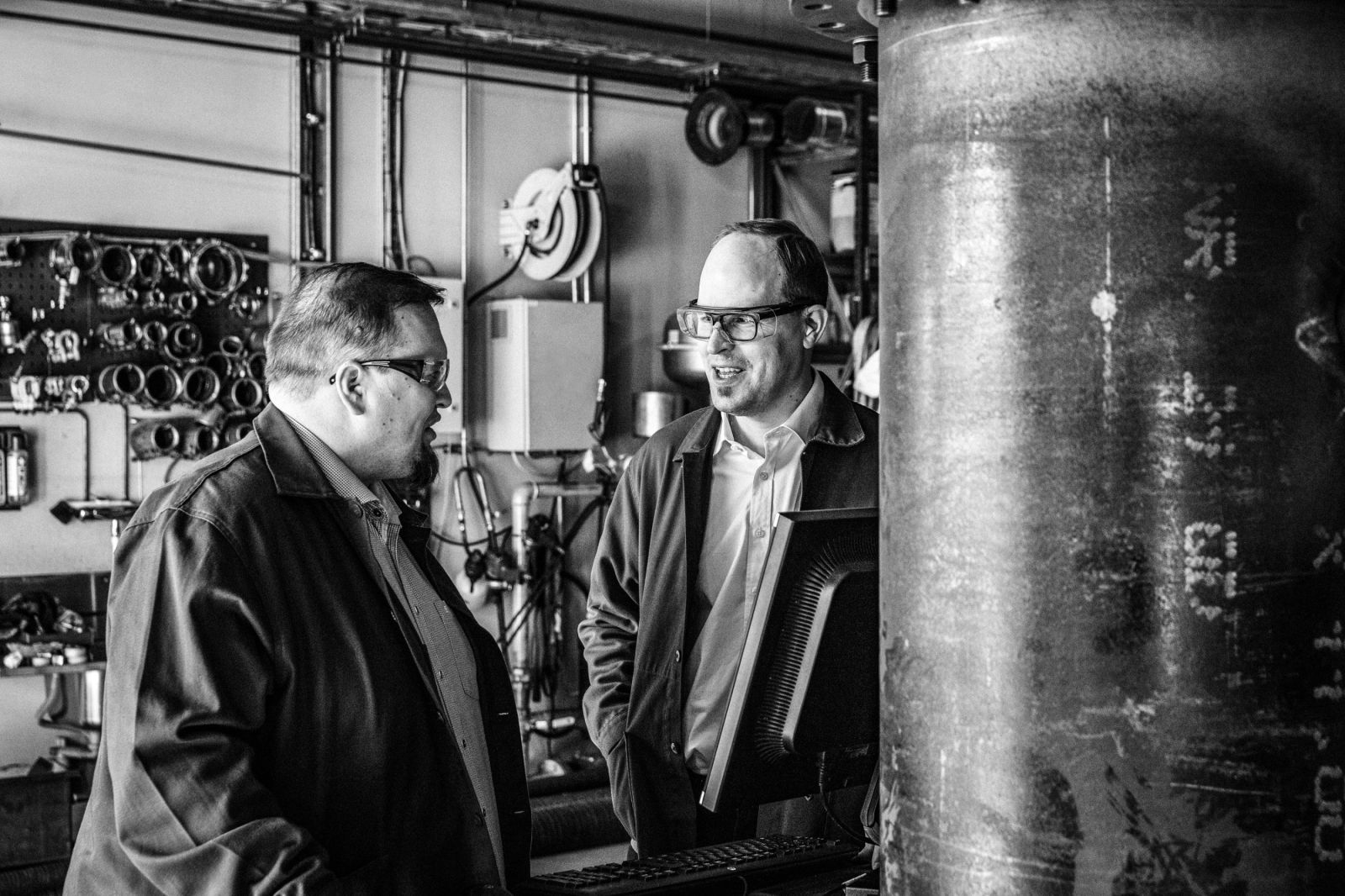
Transform your project with Vahterus Expertise
Interested in working with us? Our team of experts are ready to collaborate with you. Contact us today to embark on a journey towards cost-effective, sustainable and energy-efficient heating solutions.
Discover more of our Customer Stories
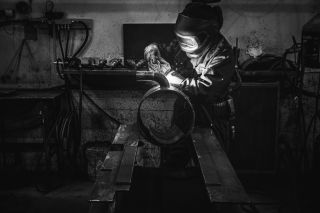
40 MW Ammonia Heat Pumps are Revolutionising District Heating in Sweden
E.ON, one of the world’s largest investor-owned electric utility service providers, installed four GEA heat pumps, each with a heating capacity of...
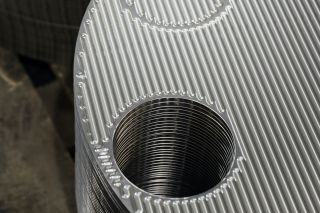
Recovery of Heat from Vapour Produces Savings at a Tyre Factory in China
A South Korean tyre manufacturing company has production facilities in Chongqing, China. The manufacturing process requires an air separator for discharging air...
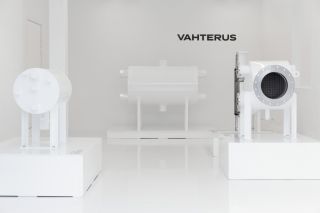
The Beauty of Being Compact: Efficient building-heat packages open doors in Canada
Leonardo Berardinelli, Vice-President Production Division at Preston Phipps Inc, Montreal...