GEA Partners with Vahterus for Groundbreaking District Heating in Gateshead
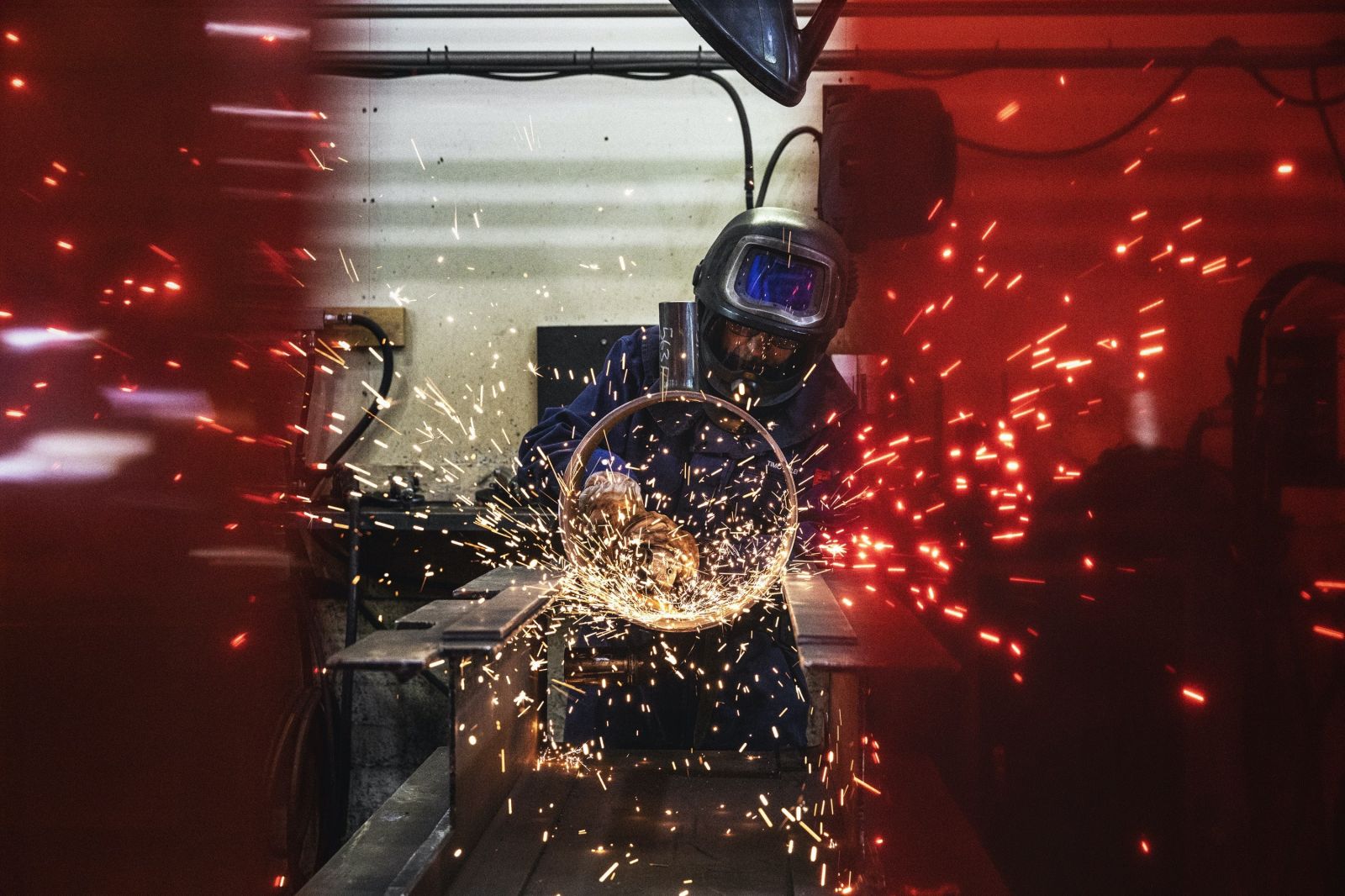
GEA has secured the order to deliver the UK’s largest capacity heat pump for district heating. 6 MW of heating energy will be provided to a heat network in Gateshead (South of the river Tyne, near Newcastle). The project has secured governmental funding and is part of the UK’s strategy for a low-carbon future.
The UK has targets to reduce greenhouse gas emissions by 57% over the 2028-32 period. Doing so will rely on a significant contribution from decarbonising heat by installing efficient heat networks in areas of high heat demand.
The goal is for heat networks to provide 17% of heat demand in homes and up to 24% of the heat demand in non-industrial business and public-sector buildings. This will require a significant increase in current growth rates and investment in heat networks. Use of heat storage and electric heat (for example from heat pumps) offers significant electricity system balancing opportunities.
This is not the first time Gateshead has taken the headlines: Gateshead Council won the Visionary Project Award from the Association for Decentralised Energy (ADE) at its 50th anniversary awards ceremony at the Science Museum in London for phase one of its district energy scheme. The special award was given in recognition of the most significant schemes of the past decade, as well as those that set the bar for the next decade of energy initiatives.
Gateshead was once the World’s largest supplier of coal, with more than 400,000 tons being shipped out in 1625, providing essential heat for households. However, the last coal mine in the area closed in 1926 and it is the tunnels dug during this time, which have since filled with water, that work as the heat source for the heat pump. So once again, Gateshead is providing essential energy for heating its homes and industry, but this time in an environmentally friendly way, which helps reduce CO2 and NOx emissions.
The water is pumped out of the mines from a depth of 70 m at a constant temperature of 15°C. The heat is abstracted from the water and returned to another area of the mine at 7°C. The low-grade energy is then transformed into high-grade heat 80°C by using an ammonia heat pump. The heating water is fed into the district heating network. By the time the water returns to the energy centre, the temperature has dropped to 65°C. The heat pump uses electricity to run, but it only uses ⅓ of the total heat output, since most of the energy (⅔) is taken from the water-filled coal mine.
The heat-pump installation consists of 2x3 MW heat pumps. For optimised performance, a two-stage compression cycle with screw compressors is used. The ground source water is filtered and pumped through Plate & Frame heat exchangers. Titanium was selected for their evaporator plates. On the heating side, several Vahterus heat exchangers in series optimise the efficiency of the heat-pump.

Ammonia was chosen as the refrigerant because of its optimal efficiency. In the given conditions, ammonia heat pumps are 10-20% more efficient than F-gas (HFC/HFO) solutions, and with the subsidy from the UK government only being available if a COP of minimum 2.9 can be achieved, F-gas was not an option for this application.
Over the last years, a lot of research into the environmental impact of using F-gas (HFC/HFO) refrigerants has been published and many environmental issues have been highlighted questioning the longevity of these refrigerants. When investing in low-emission technology, care must be taken not to create new environmental issues like polluting our rivers and lakes with TFA (a fluoride salt that is a by-product of F-gas refrigerants).
Based on the ambitions of the UK government to significantly increase district heating in the UK, we expect to see many new projects over the coming years.
Download the case study as a PDF
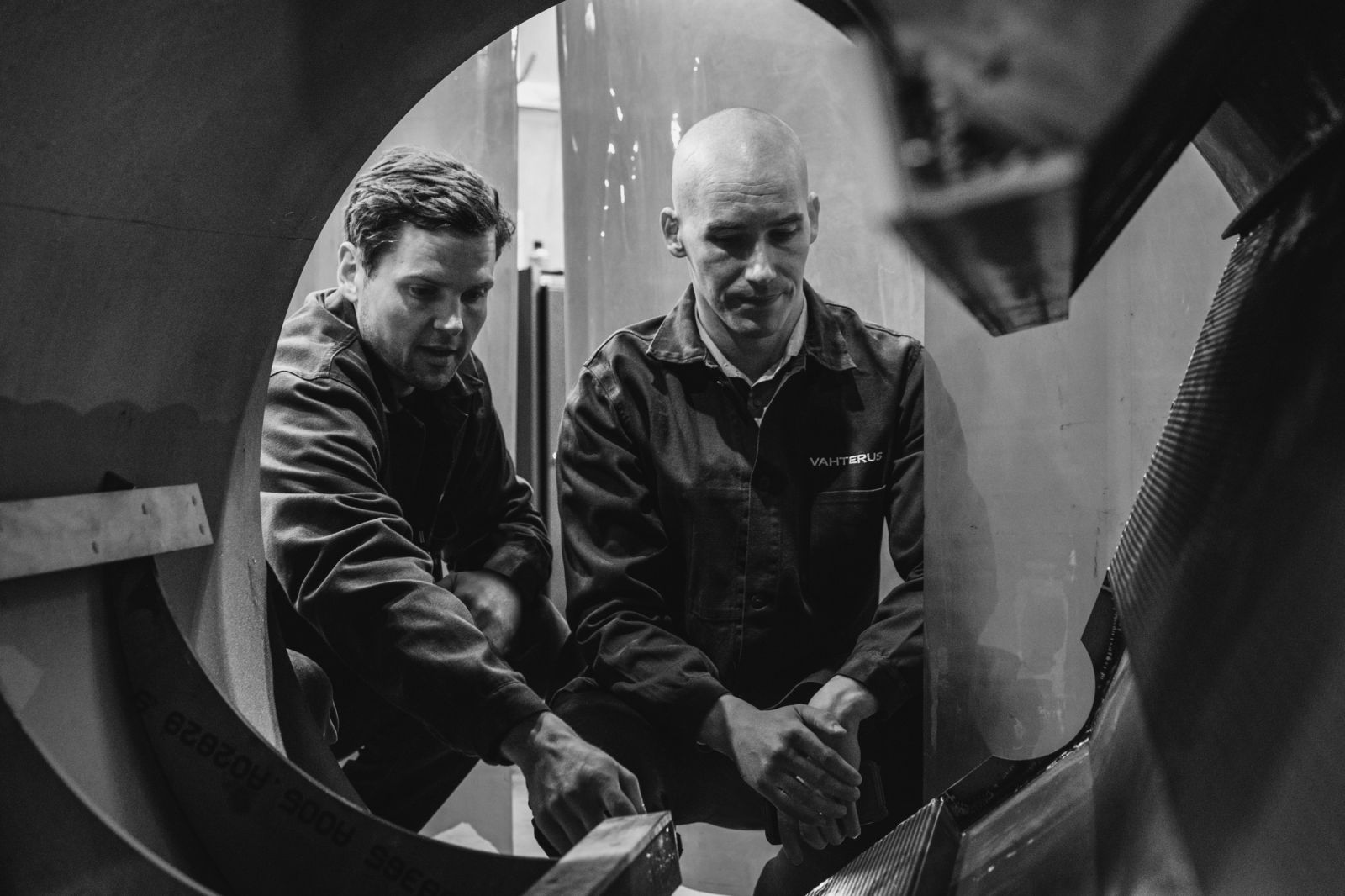
Transform your project with Vahterus Expertise
Eager to embark on your own path towards sustainable heating solutions? Our team of experts is ready to collaborate with you. Contact us today and let's shape a greener, more efficient future together.
Discover more of our Customer Stories
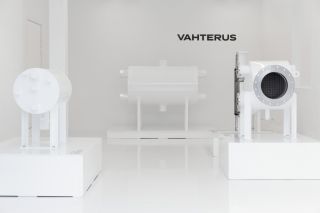
The Beauty of Being Compact: Efficient building-heat packages open doors in Canada
Leonardo Berardinelli, Vice-President Production Division at Preston Phipps Inc, Montreal...
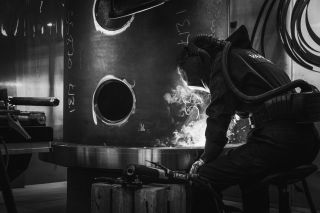
CO2 Cold Store Operates with Energy Efficiency and Sustainability in Eastern China
Yonghai Yi, Senior Sales Engineer at Vahterus China ...
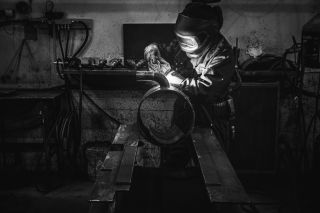
40 MW Ammonia Heat Pumps are Revolutionising District Heating in Sweden
E.ON, one of the world’s largest investor-owned electric utility service providers, installed four GEA heat pumps, each with a heating capacity of...