Fast delivery of Hastelloy Heat Exchangers to Kisuma Plant in the Netherlands
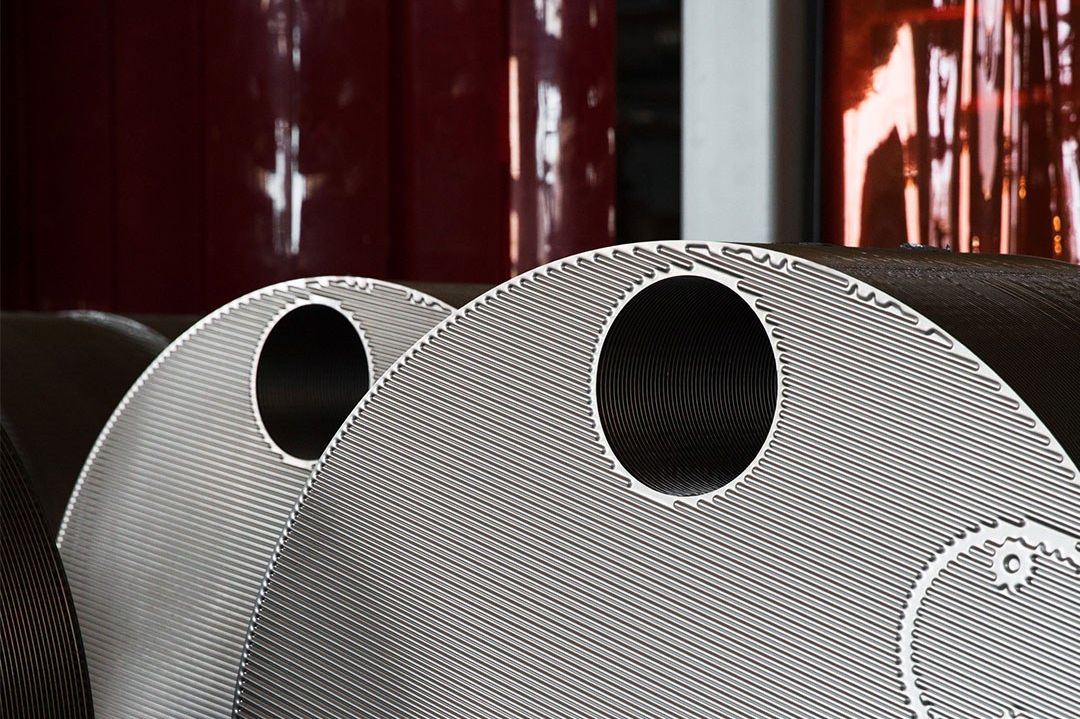
Kisuma Chemicals produces high-purity synthetic magnesium compounds and is one the world’s largest manufacturers of synthetic hydrotalcite. It’s located in the northern part of the Netherlands and is a subsidiary of the Japanese Kyowa Group, the first company in the world to succeed in the industrial synthesis of hydrotalcite.
Vahterus’s representative, Kapp Netherlands, contacted us with an urgent request for two heat exchangers for Kisuma’s plant in the Netherlands. These product coolers would replace old spiral heat exchangers, which were broken and unable to support the production needs of the plant. The most critical issue was the delivery time. Installation of the new units needed to take place within a month, during a production shutdown. The order was further complicated because the requested heat exchangers were not standard. The product being processed at Kisuma’s plant is highly corrosive, with hastelloy C-22 the only applicable material for the product side. The highly corrosive and viscous product (> 100 cP) needed to be cooled to around 100°C using process water, with the design requiring a Size 5 PSHE using C-22 hastelloy plates and a stainless-steel shell.
After receiving the enquiry, Vahterus checked the current stock levels of C-22 plates and there were exactly the right amount in stock. The rate limiting lead-time items then became the hastelloy flanges. Kapp Netherland provided contacts in the Netherlands allowing the flanges to be ordered quickly. They arrived at Vahterus’s factory just in time to fulfil the production schedule. To put these events in real time, Vahterus received the enquiry on a Wednesday; the offer was sent to Kapp Netherlands the same day, with further detail provided the following day. On Friday, Kapp negotiated with Kisuma and was able to confirm the order. Detailed engineering commenced immediately and was completed one day after receiving the order, whilst also meeting the customer’s needs for minimal layout disruption. The design was approved only a few hours after receiving the documents, and the pressing of the heat transfer plates started directly after receiving the purchase order. From receipt of the purchase order to dispatch, the delivery time was exactly 31 days.
The heat exchangers were shipped from Finland to the Netherlands in less than two days. Installing the units required special equipment and tools. The compact size of the PSHEs was a key success factor, allowing for expedient installation. All documentation was received by Kisuma the same day as the heat exchangers arrived, ready for Lloyd’s inspection and subsequent commissioning.
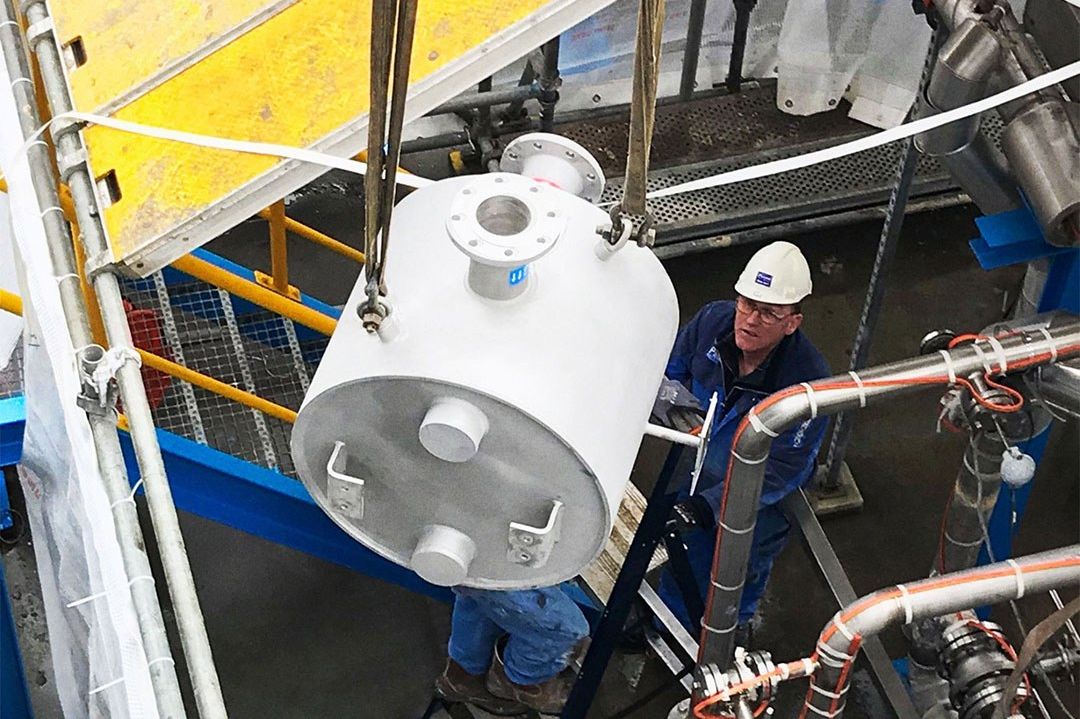
Finally, the units were insulated. Without dedication and excellent cooperation between all parties, the 31 day delivery would not have been possible. Project engineers at Vahterus and Kapp Netherlands maintained continuous contact with Kisuma throughout the process, providing photos and updates of the production process, almost every second day. In anticipation of the arrival of the heat exchangers, Kisuma built onsite dummies for prefabrication of the associated piping. All information was smoothly communicated between the three parties, allowing for a successful execution and completion of the work.
After six months of operation, Kisuma confirms that it is very satisfied with the heat exchangers, and that they are performing well within the production process.
Krista Karjala, Key Account Manager at Vahterus
Note from Ray Nahar, Project Engineer at Kapp Nederland:
”On behalf of Kapp and the end-customer, I sincerely thank Vahterus’s project team for their commitment and pro-active efforts in ensuring that everything happened according to plan. Making challenges like this happen, in the real world, makes me proud and happy to work with Vahterus.”
Download the case study as a PDF
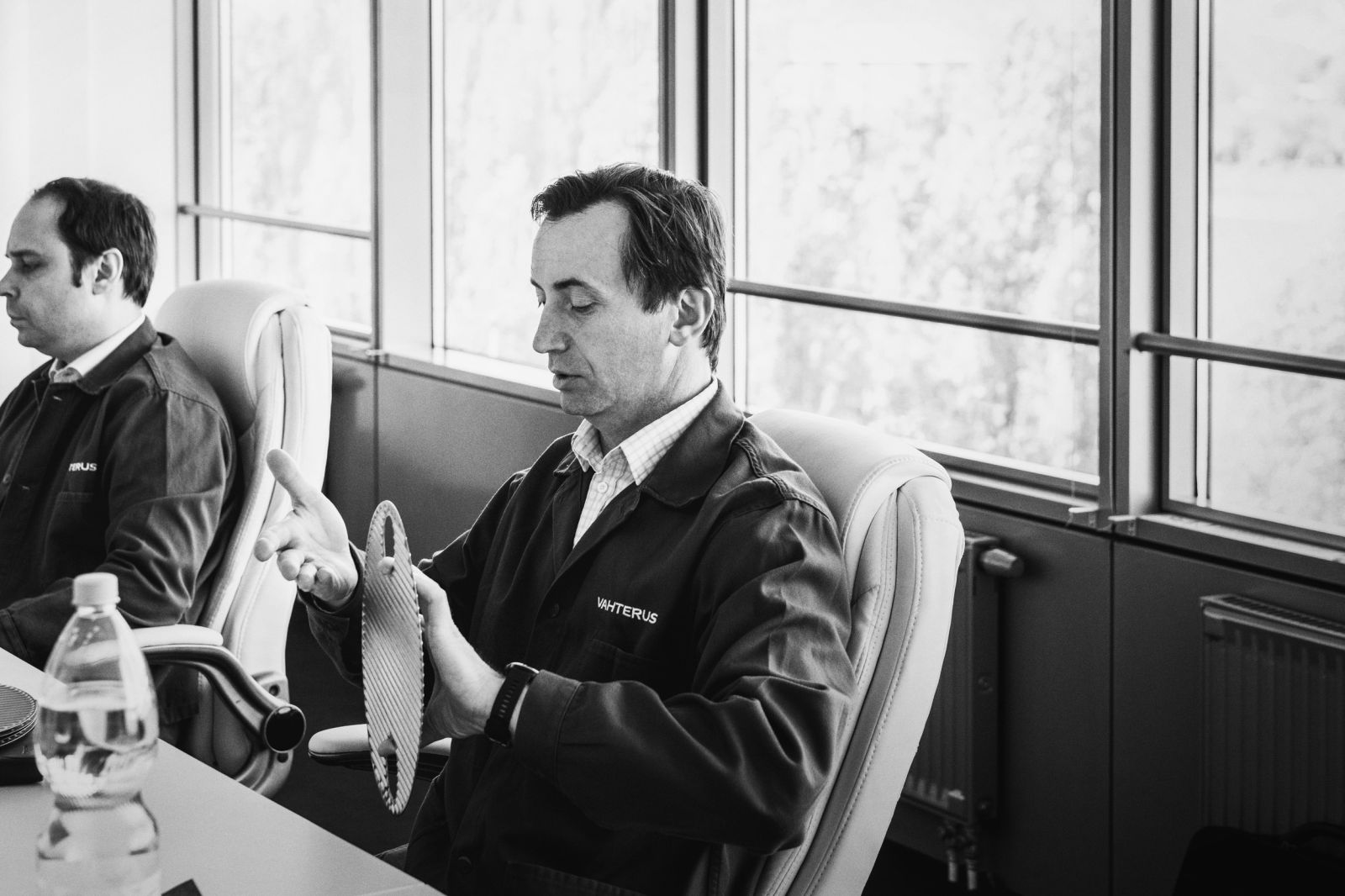
Transform your project with Vahterus Expertise
Interested in working with us? Our team of experts are ready to collaborate with you. Contact us today to embark on a journey towards cost-effective, sustainable and energy-efficient heating solutions.
Discover more of our Customer Stories
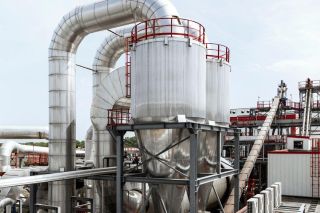
Global Challenges Drive Innovation at Pannonia Bio’s Ethanol Plant
Pannonia Bio's ethanol plant not only leads in green innovation but exemplifies collaborative success. Since 2012, the company has grown into Europe's...
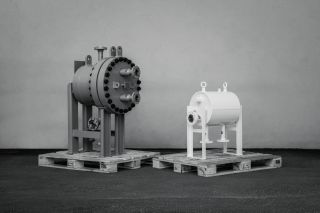
Large Reboiler Units and Heat Exchangers to Ningxia in China
A large industrial centre focusing on energy generation and the petrochemical use of mineral coal is currently being built in the region...
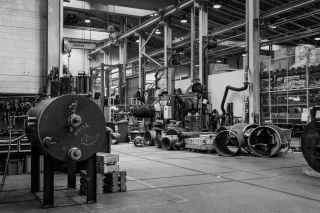
Colonial Pipeline Runs Between the Gulf Coast and the New York Harbor Area
Colonial Pipeline, headquartered in Alpharetta, Georgia, is the largest US refined products pipeline system and can carry more than three million barrels...