Entering Into Low-Carbon Economy Utilising Cold Energy Recovery
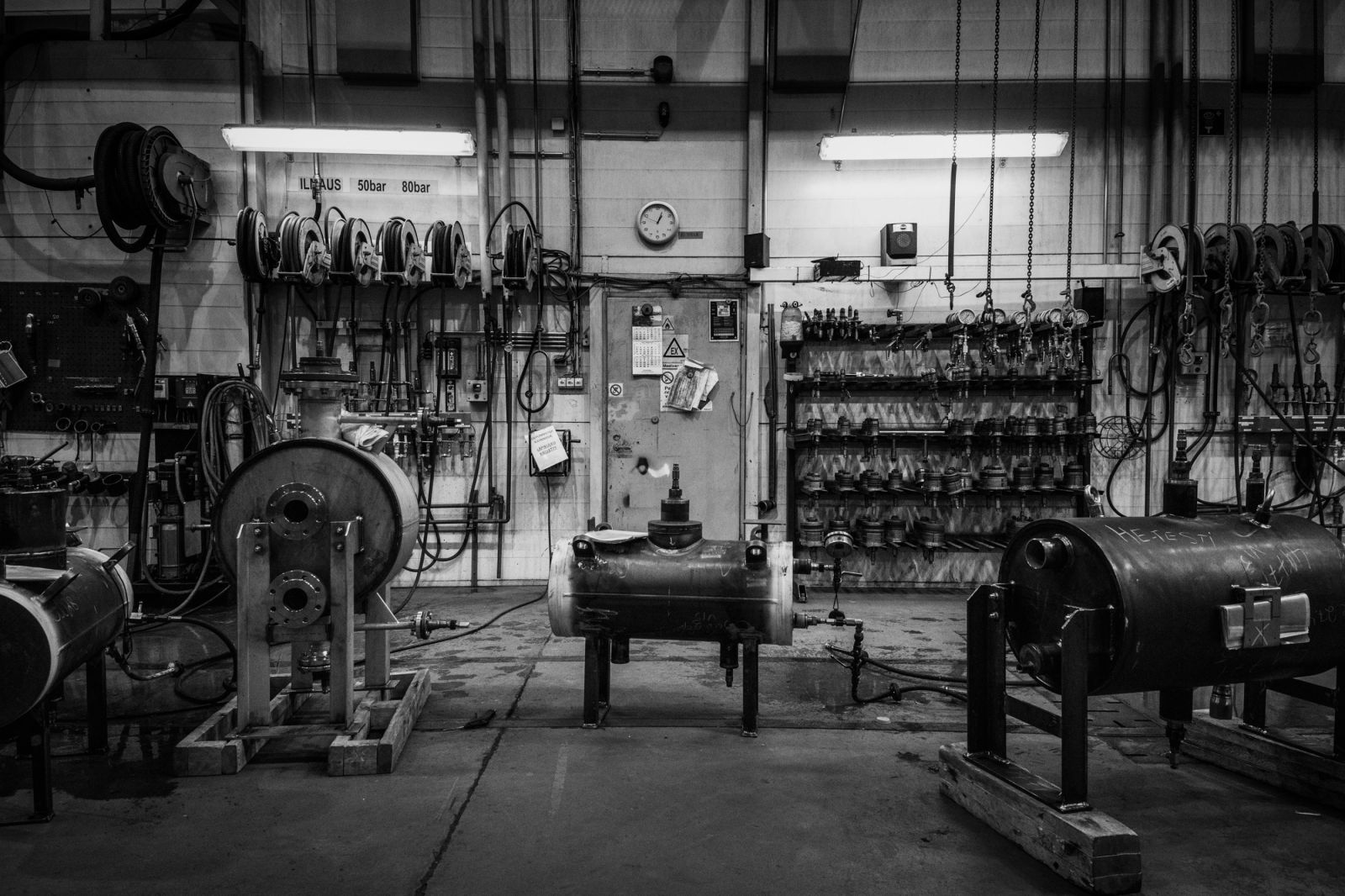
The production of alcohol amines requires large amounts of ethylene. A chemical plant in Eastern China specialises in alcohol amine production. Ethylene purchased from outside is stored at the plant as liquefied gas below –103°C. The production process, however, uses vaporised ethylene gas.
Before the recovery project, the ethylene was heated and vapourised using steam with methanol as the intermediate medium. Not only were large quantities of high-grade cold energy wasted, but the annual steam consumption was also enormous. The total capacity of ethylene vapourised was approximately 3,800 kW, which would cost about 8 million RMB (over one million Euros) per year in heating by steam.
Since glycol cold energy is needed to satisfy the cooling demands of the chemical process, this was an opportunity to utilise ethylene cold energy, which would be transferred to 50% ethylene glycol through propylene condensing and evaporating in the intermediate loop.
Propylene is a good choice of intermediate fluid to avoid glycol freezing. The cold recovery project could achieve two different cold streams of –30°C glycol and 0°C glycol for another process in which it was used directly. It could also reduce the power consumption of previous glycol refrigeration systems by about 6 million RMB per year.
In the cold recovery innovation, the major equipment comprises an ethylene vaporiser with propylene condensing, and a glycol cooler with propylene evaporating. The operating condition for the heat exchanger was demanding, since the working temperature had to be around –103°C at its lowest and the working pressure up to 38 bar(g). A small temperature approach and high heat transfer efficiency were required, as well as thermal calculating with preheating, evaporating and superheating in the ethylene vapouriser. The structure of the heat exchanger also needed to be robust to ensure stability in the ethylene gas supply.
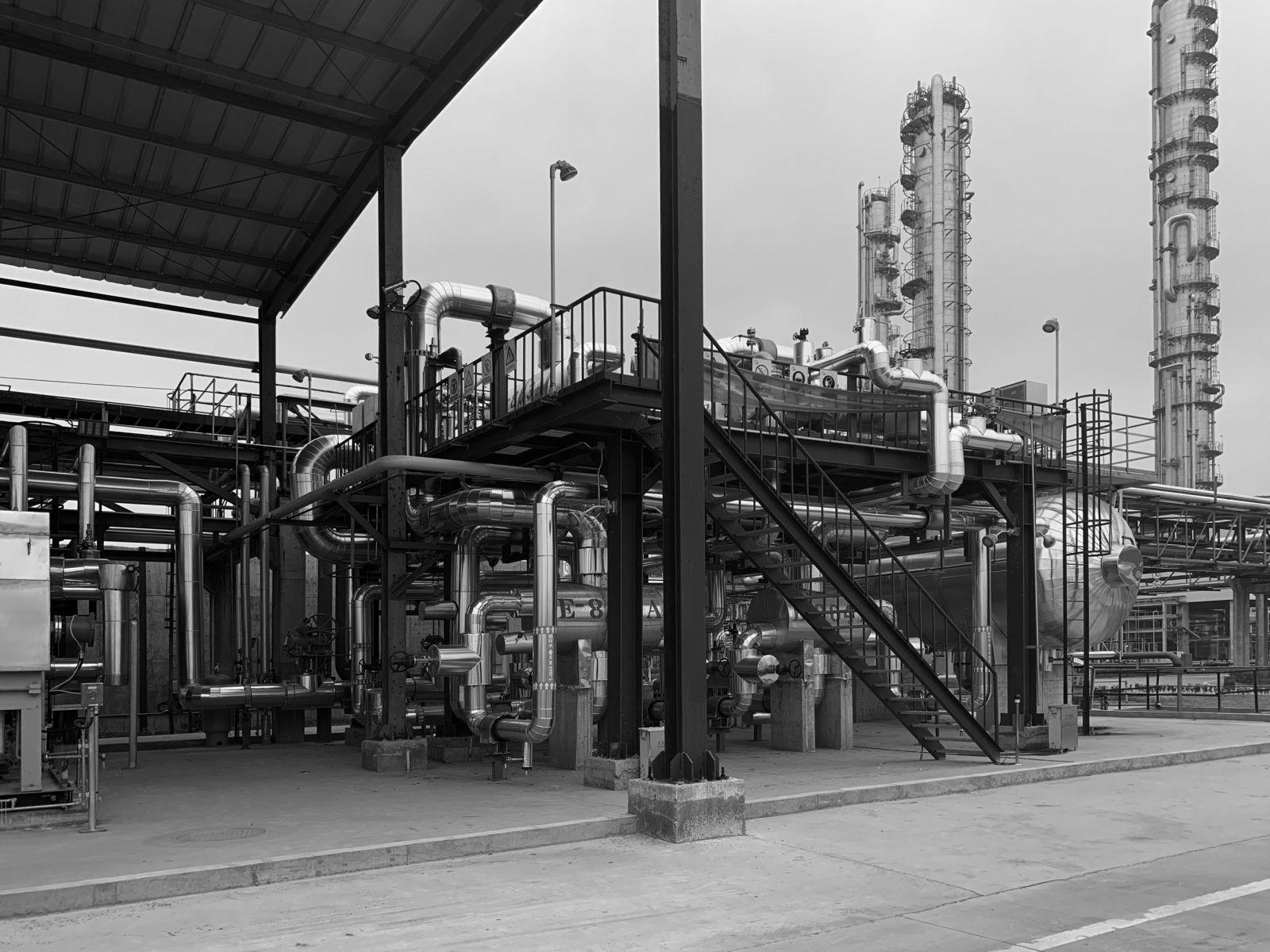
At the time of the proposal, Vahterus Plate & Shell heat Exchangers had already been proven to bear low temperature thermal shocks and high pressure shocks. In addition, Vahterus had been deeply involved in research and development over the past decades. We had accumulated many thermal calculation experiments and had successfully used a thermosiphon loop for cooling energy recovery. For these reasons, the company chose Vahterus heat exchangers.
Six units were installed in August 2018 and they have been operating since November 2018. The performance of the whole recovery project is excellent. The company has saved steam and power consumption to the tune of about 7.6 million RMB in the past six months. Energy recovery is also a meaningful way to enter into low-carbon economy for sustainable development. The benefits of this very successful heat exchanger solution will be carried over from the present user to the next generation.
Download the case study as a PDF
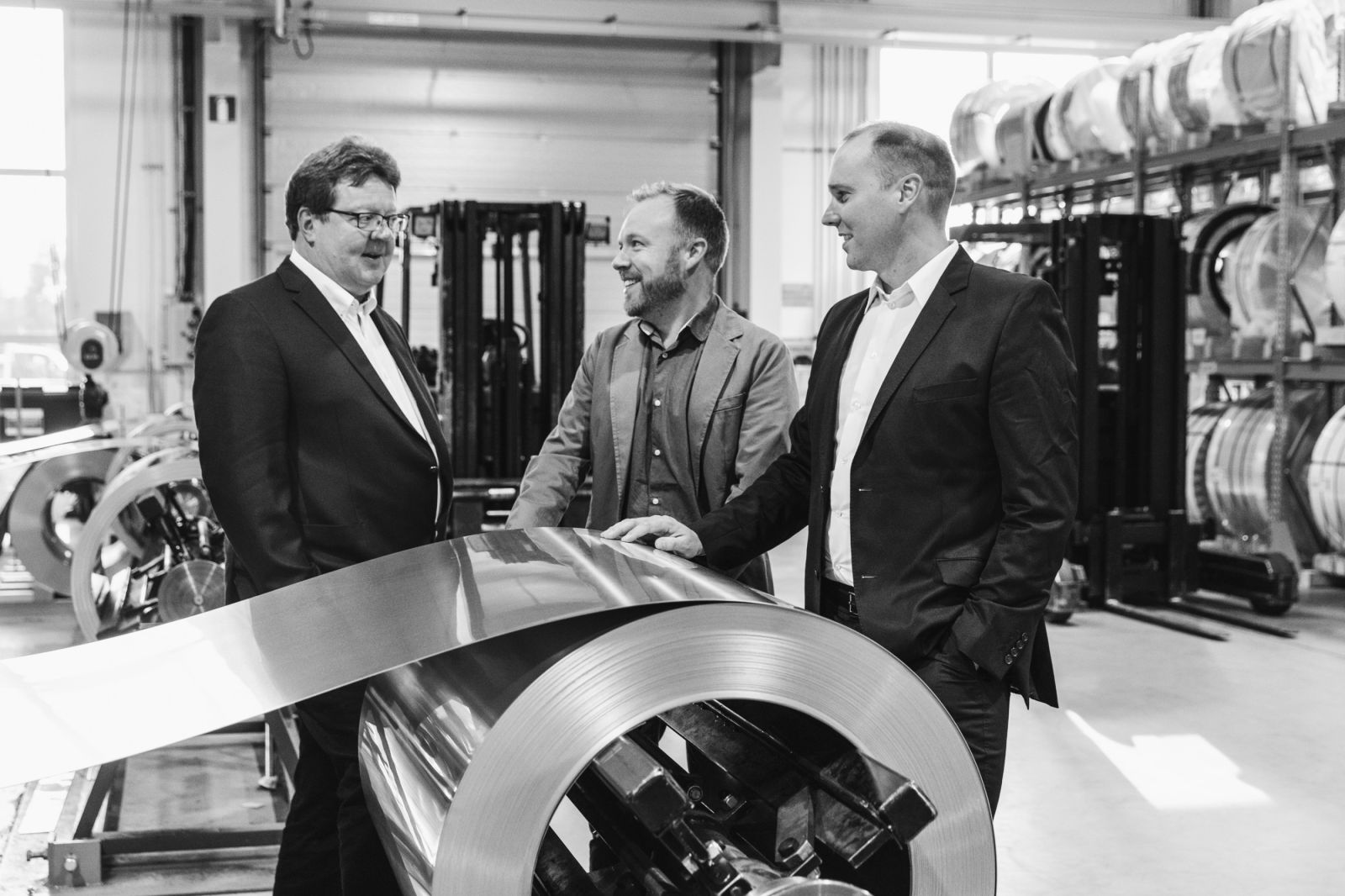
Transform Your Project with Vahterus Expertise
Eager to bring innovation to your heating project? Our team of experts are ready to collaborate with you. Contact us today to embark on a journey towards cost-effective, sustainable and energy-efficient heating solutions.
Discover more of our Customer Stories
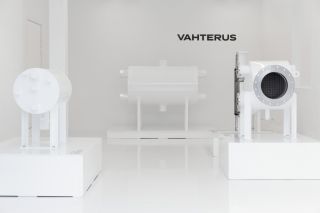
The Beauty of Being Compact: Efficient building-heat packages open doors in Canada
Leonardo Berardinelli, Vice-President Production Division at Preston Phipps Inc, Montreal...
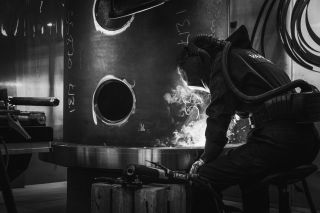
CO2 Cold Store Operates with Energy Efficiency and Sustainability in Eastern China
Yonghai Yi, Senior Sales Engineer at Vahterus China ...
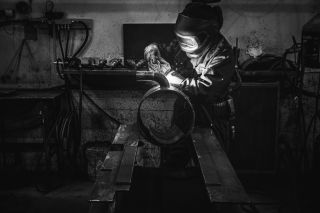
40 MW Ammonia Heat Pumps are Revolutionising District Heating in Sweden
E.ON, one of the world’s largest investor-owned electric utility service providers, installed four GEA heat pumps, each with a heating capacity of...