Slimmer Sibling for Vahterus Plate Family
The family of Vahterus heat transfer plates continues to grow with a new plate. The slimmer plates, launched in mid-2018, use the shape of an athletics field, combined with the same optimal corrugation options as the Vahterus round plates.
Valtteri Haavisto, Customer Service Director at Vahterus
The family of Vahterus heat transfer plates continues to grow with a new plate. The slimmer plates, launched in mid-2018, use the shape of an athletics field, combined with the same optimal corrugation options as the Vahterus round plates. Plate configurations are designated SH or SL depending on the corrugation angle, where stands for ‘slim’, and H or L for ‘high’ or ‘low’ heat transfer plate corrugation options. This new plate type is designed for application in gas heating and cooling, but alternative uses are certainly possible in the future. The Vahterus slim plate has a longer flow path on the plate side and a shorter flow path on the shell side, which leads to a low-pressure drop on the gas side, and optimal heat transfer and performance on the plate/liquid side. The default design utilises cross-flow configuration, maintaining the equivalent shell designs used with traditional PSHEs.
The tests made by Vahterus’s R&D have proved that the slim plate provides an effective heat-transfer solution in gas cooling and heating applications, whilst at the same time maintaining low gas side pressure drop. Vahterus is confident that this will provide a very effective heat transfer solution in gas-based applications, notably for heat-recovery cases. In this first stage of development, the new plate series will have a design pressure range of 6–60bar(g) (depending the plate size), relevant to the design temperatures typical of such applications. Thermal design tools, as well as all manufacturing capabilities, are ready to go for the new heat-exchanger type. In the initial stages, plate sizes 3 and 5 will be available, first deliveries taking place later this year. The Vahterus Sales Team is happy to tell you more about these new developments, and how they can optimise your processes.
Testing with HTRI in Navasota, Texas
Thomas Lestina, Senior Vice President Engineering at Heat Transfer Research
As Plate & Shell Heat Exchangers gain acceptance in the process industry, many potential users are seeking validated performance data of the latest commercial plate technology so that they can be assured of adequate operation. HTRI, a leading source of process heat-transfer technology, is working with Vahterus to assess the PSHE performance for liquid-liquid and boiling service.
Vahterus shipped two test exchangers to HTRI’s multimillion-dollar Research & Technology Center (RTC) in Navasota, Texas, USA. HTRI installed one in the Liquid-Liquid Heat Exchanger Test Unit for water-water tests and the other in the Prototype Test Unit for boiling tests with pure hydrocarbons and hydrocarbon mixtures.
From the water-water test results, HTRI developed and validated a heat transfer and pressure drop model for single-phase service. The boiling tests allowed to study the impact of nucleate and convective boiling mechanisms, and to investigate corrections needed for mixtures.
The HTRI testing demonstrates that the PSHE is a compelling alternative, not only to Shell & Tube exchangers but also to other plate technologies such as gasketed Plate & Frame exchangers and welded rectangular plate exchangers. The test results are documented in two reports soon released to HTRI members. Working closely with Vahterus, HTRI is continuing its analysis of the test units with the development of a CFD model of the corrugated plate surfaces. The high-fidelity model provides insight into factors that affect flow distribution and pressure drop, leading to improvements in overall performance.
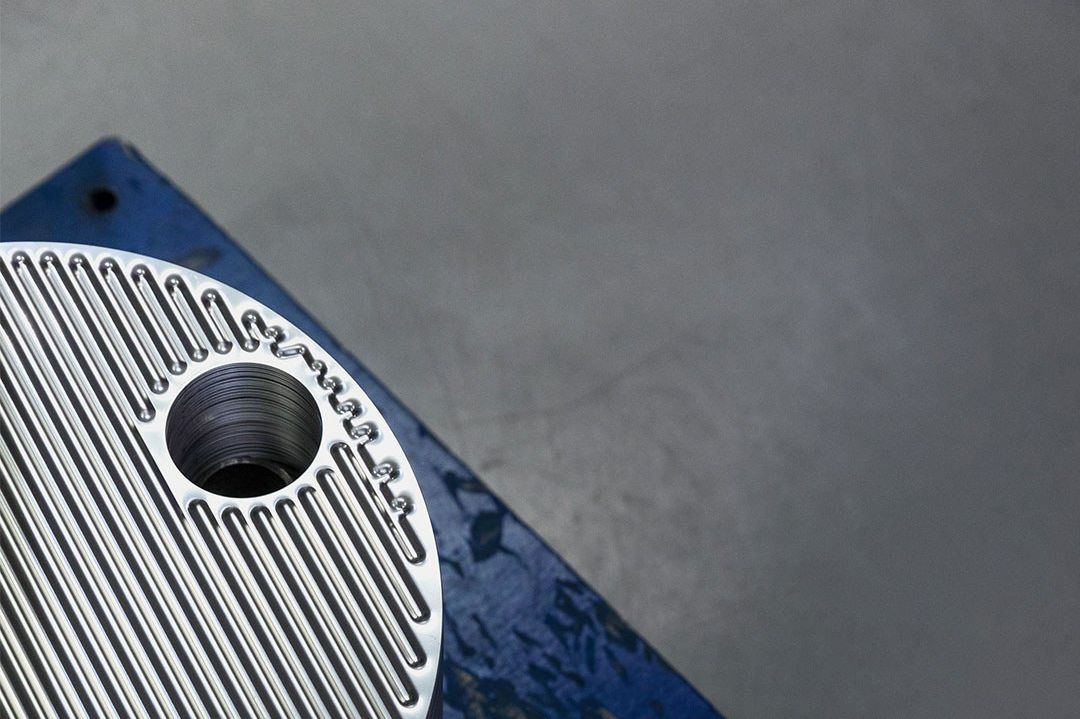