R&D News: Understanding the Limits in Cold Recovery
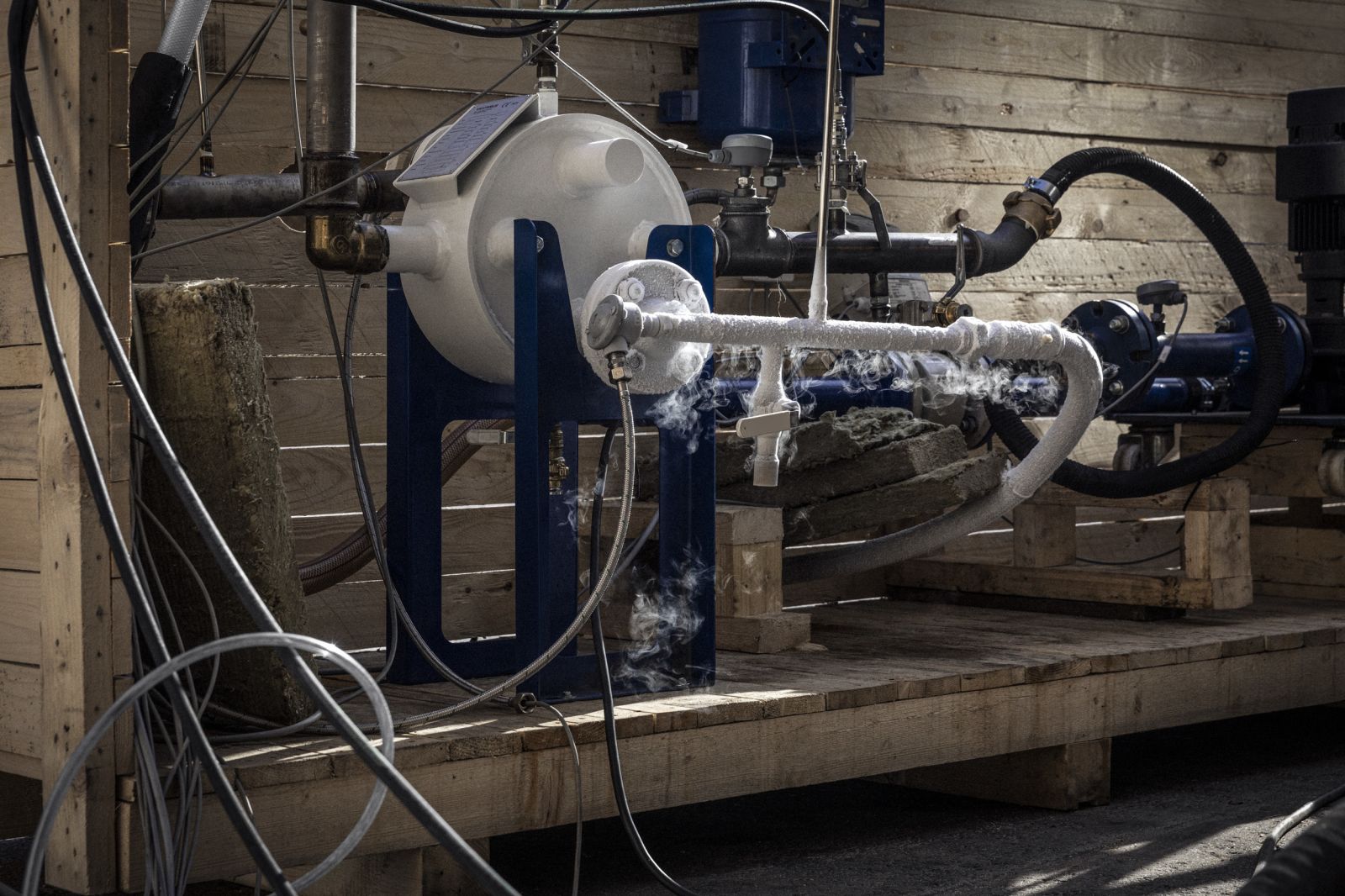
Vahterus’ R&D team has conducted a series of tests to understand the behaviour of ethylene glycol in freezing conditions. This is one of the most important factors to take into account when designing a cold-recovery heat exchanger.
Cold can be effectively recovered when cryogenic liquids are vaporised into gas. Such evaporation offers a great deal of energy at very low temperatures. For example, vaporising Liquified Natural Gas (LNG) releases 860kJ/kg of cooling capacity from -160°C to an ambient temperature. Instead of dumping it into the air or sea, that energy can be utilised in applications requiring cooling.
Low temperatures can be used in cold-storage facilities, freezing rooms and air conditioning, or simply anywhere that requires refrigeration. However, cryogenic temperatures are challenging for brines like glycols that are at risk of freezing when cooled down in the heat exchangers that vaporise LNG.
Vahterus’ tests investigated how to avoid brine freezing. One target was to identify when and how the glycol starts to freeze. Liquified nitrogen was vaporised at about -180°C, and 50% ethylene glycol was used as a heating medium. The freezing temperature of such glycol is -37°C and the burst temperature -51°C. This means that at -37°C, ice crystals are created and at -51°C, the glycol will be solid ice.
The finding of the tests was that good heat-exchanger design makes it possible to use very low glycol outlet temperatures, avoiding the risk of freezing. Even the cold side inlet temperatures are less than the freezing point of glycol.
Low glycol outlet temperatures can be utilised in air conditioning or cold rooms. If colder temperatures are required, it is best to implement an intermediate loop that prevents freezing. Freeze-resistant intermediate fluids such as R134a or ethane could be used.
The tests continue, and will reveal new possibilities when working with extremely cold temperatures.
Valtteri Haavisto
Customer Service Director
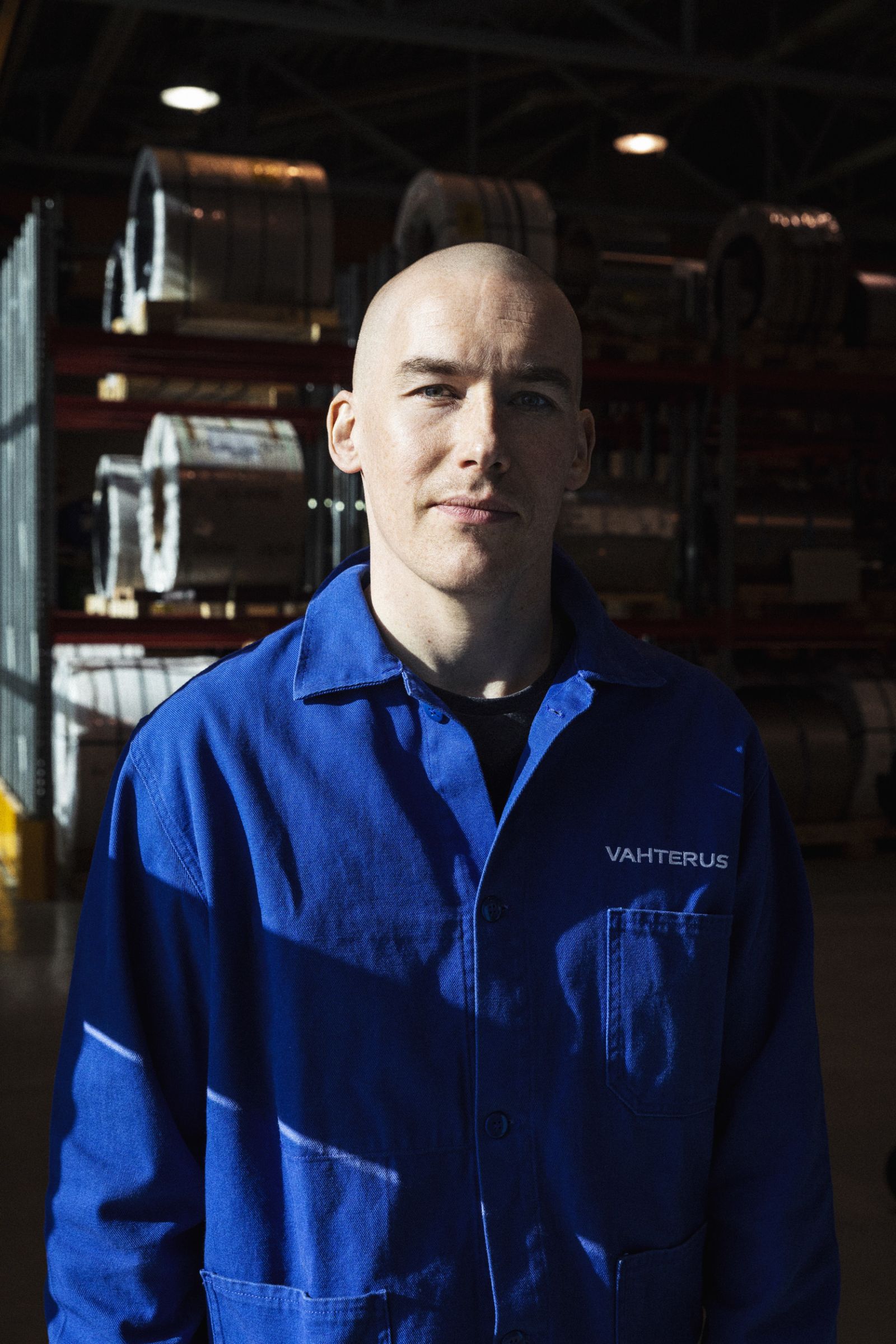
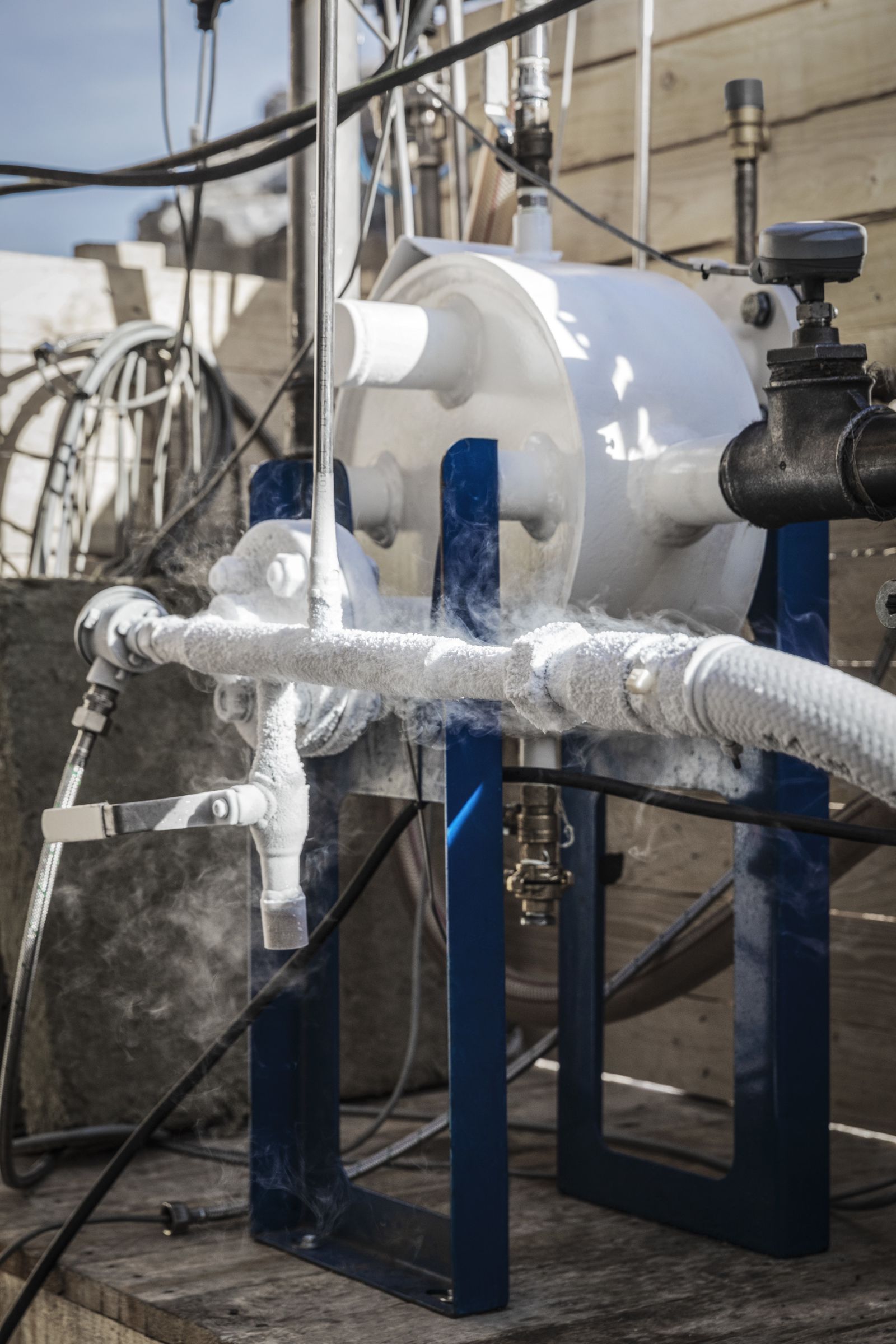