Benefits of Vahterus Plate & Shell Technology in LNG Applications
The use of natural gas around the world is growing, and in energy production the traditional oil and coal are expected to be eclipsed by natural gas in the coming years. With the introduction of the European Sulphur directive and other regulations across the world, LNG has recently gained increased relevance as a fuel source for ships, due to its relative environmental friendliness. With an energy density somewhat comparable to oil, essentially non-existent particle and sulphur emissions, and very low NOx emissions, liquefied natural gas is seen by many as a competitive modern fuel. Numerous cruise liners and passenger ferries have already been converted, and many new ships are built with LNG compatibility in mind. One example is the conversion of the container ship Wes Amelie to use LNG as a fuel source, where Vahterus, in collaboration with TGE Marine Gas Engineering Gmbh, provided the necessary skid and fuel system.
The transportation of natural gas has therefore become an increasingly important issue. While natural gas can be pumped through pipelines, these pipes can reach only specific locations and require everything from environmental planning to land-use permissions and licenses throughout the entire pipeline. A common alternative is liquefaction. LNG, which is over 400 times denser than the gaseous form, allows it to be stored and transported much like other liquid products. This can be both in bulk for large carrier vessels between terminals, and in smaller quantities by trucks from terminals to small-scale end users such as factories or refuelling stations.
However, before LNG can be used, it must be re-gasified and heated back to ambient temperatures. Unlike bulky Shell & Tube units or ambient-air LNG vaporiser towers, Vahterus Plate & Shell technology allows for the vaporisation and superheating of LNG from its storage temperature directly to ambient and above in a single, small unit. The compact size of the Vahterus Plate & Shell Heat Exchanger is a major advantage for any vessel conversion, since it leaves more space in the engine room for other necessities, such as instrumentation and piping. As the materials required for cryogenic operations tend to be stainless steel, the small size of Vahterus’s products (in comparison to Shell & Tube heat exchangers) usually translates to a cost advantage as well.
The same applies for heating or cooling boil-off gas, a problem for which any cryogenic liquid storage tank, no matter how well insulated, has to account, due to relatively warmer ambient conditions. Vahterus has extensive experience in both cargo condensing and heaters to make use of naturally evaporated gases. Vahterus units are a well-proven technology on marine and floating systems, and for cryogenics.
Due to the fact that the round plate is highly resistant to thermal stresses and able to handle large temperature differences between the plates, cold recovery for HVAC or freezer systems becomes possible, using glycol and similar fluids as a secondary circuit. The Plate & Shell Heat Exchanger is well suited to these applications and can greatly increase the overall efficiency of a small-scale LNG system.
Another alternative is to use an indirect system, where an intermediate thermosiphon loop is created. Driven by gravity and thus requiring no pumps, this loop contains some materials that are evaporated and condensed in a continuous cycle. With such an indirect system, it is possible to use a wide range of heat sources for LNG vaporisation: seawater, engine coolant water and many other possible alternatives exist. A custom-made indirect system is designed to fit a customers’ needs, and is usually no larger than two or three metres tall.
The overall duty of these systems is no more limited than any Vahterus heat exchanger. The range of delivered units is wide, beginning with small evaporators on board tugboats, where LNG use can be only 100 kg/h or even less. Others are helping to fuel large ferries or power systems, providing vaporisation of thousands of kilograms per hour of LNG. On the high end of the scale, Vahterus can manufacture even larger units, which are in service in LNG terminals where major re-gasification operations of over 10,000 kilograms per hour can take place, which have boil-off gas handling corresponding to their large-scale storage.
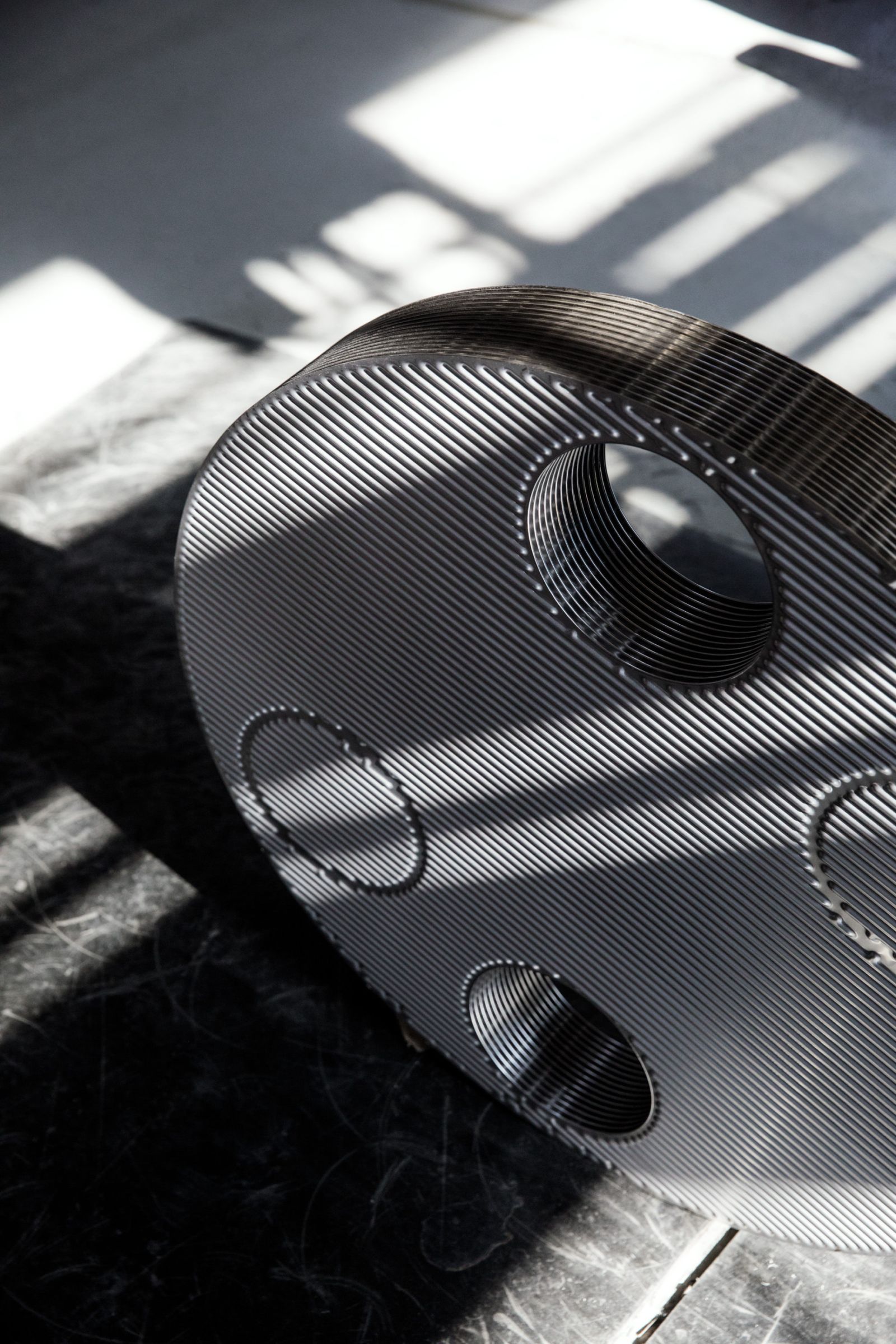